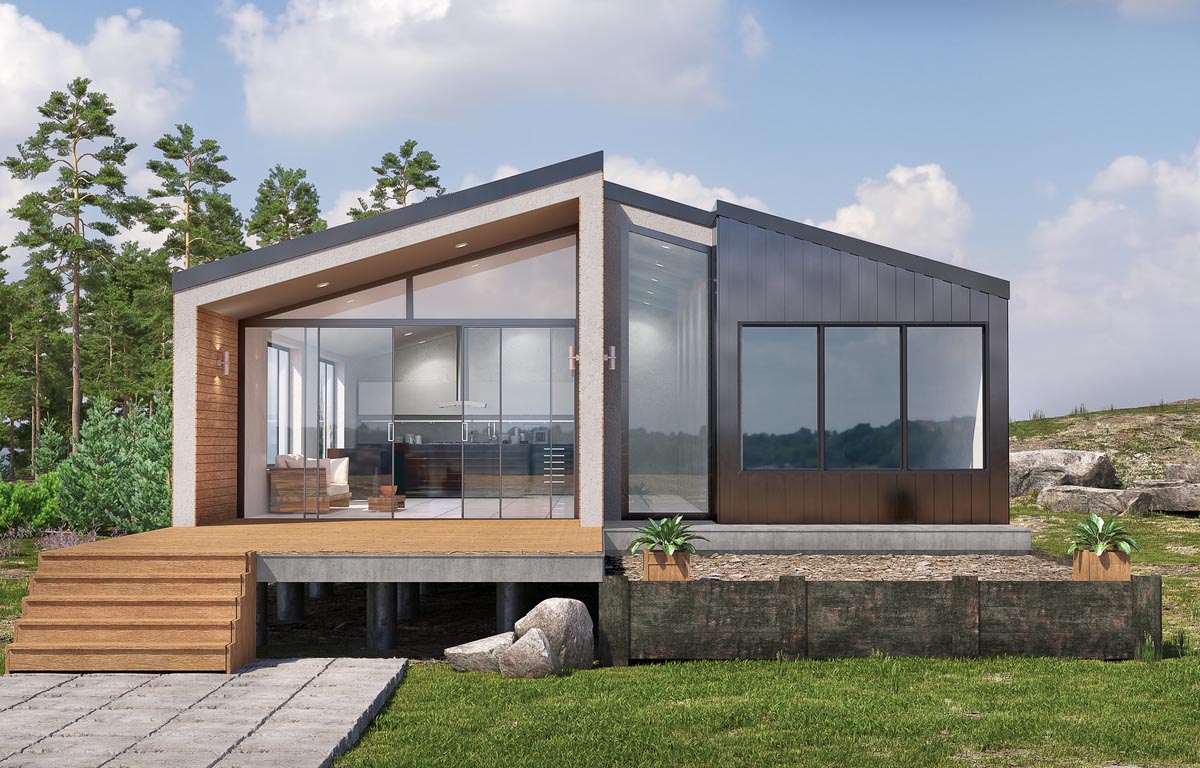
We may earn revenue from the products available on this page and participate in affiliate programs. Learn More ›
While modular homes are not yet as popular as traditional stick framing, the modular home industry is growing quickly. More and more folks are seeing the benefits of ordering pre-built homes assembled in climate-controlled factories. Tight tolerances, reduced waste, and fast move-in times give them plenty to think about, and the potential cost savings help bolster the case as well.
But even after reading modular home manufacturers reviews, it may be hard to choose the right manufacturer. This guide aims to help home shoppers by compiling all of the important information and detailing the most critical factors pertaining to modular home shopping. It will also help home shoppers who are considering which of the best modular home manufacturers will best suit their needs.
- BEST OVERALL: Clayton Homes
- ECO-FRIENDLY PICK: Deltec Homes
- BEST FOR CUSTOM HOMES: Impresa Modular
- BEST MODERN DESIGNS: Connect Homes
- ALSO CONSIDER: Commodore Homes
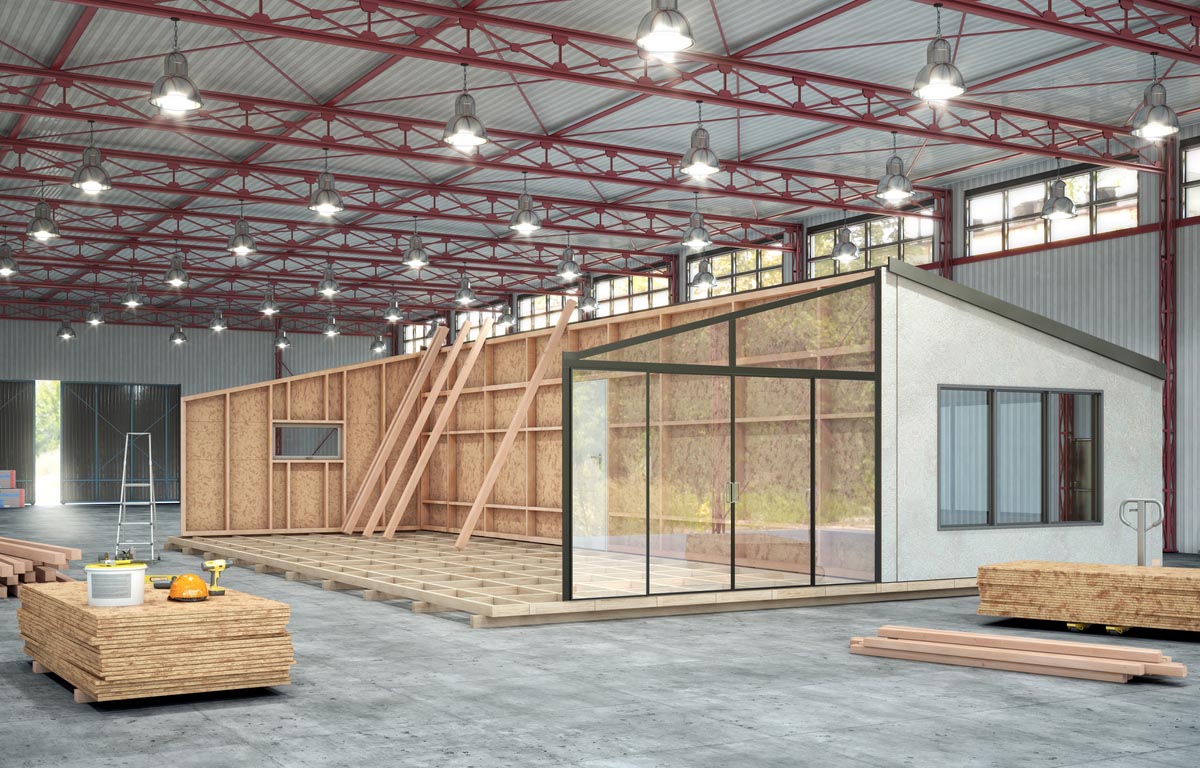
What to Consider When Choosing One of the Best Modular Home Manufacturers
Depending on the area in which a home buyer lives, there may be many manufacturers to choose from. For this reason, it becomes extremely important that they do their research on modular homes and the process.
Prefab vs. Modular vs. Stick-Built Homes
Prefab. Modular. Stick-built. What does it all mean? All of these designations refer to structures built and assembled with specific techniques.
- Prefab: Short for prefabricated, prefab is a term used to describe homes built in factories and delivered to home sites. They include mobile and manufactured homes (those built on metal chassis and delivered to the site), modular homes built in two or more sections, or even kit homes assembled and disassembled in a factory and shipped to the customer.
- Modular: Modular homes are factory-built homes that are shipped in two or more sections and placed on a permanent foundation. These homes come in a wide range of sizes and designs.
- Stick-built: Homes built on-site, board by board, are known as stick-built homes. All of the framing and finishing is performed on-site. This is the most traditional and popular method of construction, though it’s slowly giving up its share of the home-building market to modular construction.
Price Range
The average modular home ranges between roughly $40 to $80 per square foot as a base price and $100 to $200 including installation. Smaller homes with builder-grade features like vinyl flooring and laminate counters will cost near the lower end of the range. Large models made from several sections that include higher-end finishes will cost toward (or more than) the top of that range.
All in with site preparation, utilities, taxes, fees, and more, customers can expect to pay between $72,000 and $144,000 for a 1,800-square-foot home. This is less than the cost to build a similar size and style stick-built home, which costs between $180,000 and $360,000.
Home buyers will want to note that these costs include the price to purchase the land. And specialized multi-family modular home manufacturers may fall into entirely different price points due to thicker firewalls and framing.
Customization Options
Modular homes follow specific plans, and manufacturers typically offer anywhere from just a handful to 20 or 30 floor plans and designs. However, many builders also allow home buyers to customize the floor plan to best suit their needs.
Also, beyond changing floor plans, almost all modular home manufacturers offer custom finish options. For example, a shopper may be able to choose between carpet, vinyl, hardwood, or tile for their flooring. Similarly, they’ll be able to opt for granite countertops over laminate if they should choose and their budget allows. Siding and roofing colors are customizable, as are entry doors and add-ons like decks and porches (which are built on-site).
Financing Options
In general, financing a modular home is fairly similar to financing a stick-built home. Buyers can go the route of traditional mortgages, construction-to-permanent loans, or personal loans. The exception to this rule is that some lenders will not offer traditional mortgages on modular homes.
Some modular home companies actually partner with lenders specializing in modular home financing. While interest rates may be higher than those through a traditional lender, this financing option allows the buyer to build a home, move in, and refinance the home through a standard lender, if they wish.
Construction and Shipping Times
Modular homes are typically much faster to construct than stick-built homes. Materials are generally delivered to one location (the factory), and tools are always available where they need to be. Climate control also allows the crew to work more comfortably and minimizes any weather-related delays.
This efficiency allows the typical manufacturer to build a modular home in 3 to 4 months of actual construction compared to the 7 or 8 months required to build a stick-built home. However, luxury modular home manufacturers may take significantly longer.
Shipping times will vary based on several factors. The home site’s proximity to the facility, the number of sections, and freighting availability all play a part. Folks that live outside of the factory’s designated shipping area may have to pay additional fees to have their homes delivered as well.
Site Preparation and Installation
Site preparation is the responsibility of the property owner, not the manufacturer. This means that any excavation, septic, well drilling, electrical service, and foundation work need to be performed before the modular home is delivered. In many cases, the homeowner will hire a general contractor to handle these tasks.
Installation is another story. Some modular home manufacturers have their own crews who install the sections of homes, while other manufacturers may hire the job out to contractors. Homeowners might also be responsible for finding a crew. In any case, installation may account for $25,000 to $50,000 of the project.
Warranties
All home builders are mandated to provide a minimum warranty on materials and labor. The mandated period is usually 1 year regardless of whether the home is stick-built, manufactured, or modular. However, some modular home builders offer extended warranties that may cover the home for between 2 and 10 years.
Also, home buyers will want to understand that all of the appliances and mechanical systems in the home will carry their own warranties. The homeowner will likely receive a folder full of manuals and warranty information upon the final walk-through with the manufacturer or contractor.
Home buyers will want to know that it’s not uncommon for modular home customers to call their manufacturer within the first few months for small issues, as little snags are normal. The manufacturer will typically send someone to the home to repair or resolve the issue. However, this is why it’s important that the manufacturer offers excellent customer service.
Our Top Picks
With all of that background on choosing the best modular home manufacturer, it’s time to get down to business. For shoppers who’d rather not perform an internet search for “local modular home manufacturers,” here is a list of modular home manufacturers that are trusted options.
Best Overall
Clayton Homes
Pros
- Relatively fast construction and installation times
- Easy-to-use search tool for land for sale
- Flexible 5- and 10-year extended warranties available
- Winner of multiple 2022 Manufactured Home Institute Excellence in Manufactured Housing Awards
- Comprehensive home buying and homeownership resources
Cons
- Somewhat limited online home search filter functions
- Service area: Nationwide
- Price per square foot: About $66 to $115 before customizations
- Construction and installation time: 4 to 6 weeks from ordering until delivery, 2 weeks for installation
- Warranties: 1-year limited warranty; 5-year and 10-year warranties available for purchase
Why It Made the Cut: Between fast start-to-finish times, flexible warranties, and tools to navigate the home buying and ownership process, Clayton Homes is a top modular home manufacturer. Home buyers looking to balance options, price, and speed might consider going with Clayton Homes. This modular home builder offers a wide range of modular homes, some of which start at around $60 per square foot before customizations. Clayton services the entire nation and is the recipient of multiple 2022 Manufactured Home Institute Excellence in Manufactured Housing Awards. One of the biggest benefits of going with a Clayton home is the time to completion. In most cases, Clayton Homes can be ready for moving in within 8 weeks, including installation. For folks who don’t own land already, Clayton’s online search tool will help them locate land in their desired area. Each home from Clayton Homes comes with a basic warranty, and homeowners can upgrade their coverage to a 5- or 10-year plan if desired. Homeowners will notice that the online home search filter functions are limited. However, the resources and tools that Clayton provides during the home buying and ownership process can prove invaluable, including blog posts and articles through the company’s “Studio” portion of the website.
Eco-Friendly Pick
Deltec Homes
Pros
- Improved home comfort, efficiency, and resilience due to proprietary building practices
- Fast construction and installation times with Deltec Express line
- Certified B Corp company with high social and environmental standards
- 80 percent of production waste diverted from landfills
Cons
- Potential for relatively long 6- to 9-month construction and installation times
- Service area: Nationwide and overseas
- Price per square foot: $250 to $500
- Construction and installation time: 6 to 12 months total
- Warranties: 1-year warranty on materials and workmanship; optional 10-year coverage for structural defects
Why It Made the Cut: With unique designs and an eye for energy efficiency, Deltec Homes could be a great choice for folks looking for an eco-friendly modular home. Modular construction is relatively eco-friendly to begin with, but Deltec Homes takes it a step further. Because the company uses proprietary building practices such as super-insulated walls and trusses, a Deltec home is potentially three to five times more airtight than typical buildings. And, by focusing on natural comfort from solar heating and passive cooling, Deltec Homes has been recognized for innovation by the U.S. Department of Energy. Deltec Homes is a certified B Corp, cementing its commitment to environmental and social responsibility. Deltec offers several home styles, including the brand’s relatively traditional Renew line and its advanced 360-degree line. To take energy efficiency even further, the shell packages are built with 100 percent renewable electricity, and Deltec reduces waste by 80 percent by using panelized construction techniques. Keep in mind that this does translate to higher prices per square foot ($250 to $500). While there is the potential for very long lead times (9 months or more), Deltec does offer its Express line, which can reduce waiting by 6 to 9 months.
Best for Custom Homes
Impresa Modular
Pros
- Fully custom home designs available
- Collaborative custom-design process
- Wide range of preplanned home styles available
- Interactive online design tools
Cons
- No warranty information available
- Service area: Nationwide
- Price per square foot: About $200 to $245
- Construction and installation time: 3 to 4 months for construction and installation
- Warranties: Not specified
Why It Made the Cut: When it comes to customization, Impresa Modular offers an impressive range of floor plans, choices, and design tools. Modular homes have a reputation for being basic or boring, but with Impresa, that’s just not the case. This custom modular home manufacturer allows shoppers to design their homes from scratch using the company’s interactive design tool, HomeStyler. Impresa’s collaborative custom-design process ensures the customer is getting exactly what they want, and prices range between $200 and $245 per square foot. But Impresa Modular is good for more than just custom builds; the brand has hundreds of available floor plans that customers can choose from. Aside from the mandated 1-year warranty, there is no warranty information listed on the site. But the 3- to 4-month lead time from construction to installation is very fast—especially for a custom build.
Best Modern Designs
Connect Homes
Pros
- Unique, eye-catching modern designs
- Streamlined collection of home floor plans
- Comprehensive pricing breakdowns
Cons
- No warranty information available
- Somewhat user-unfriendly website
- Service area: Contiguous U.S. with additional cost for sites more than 60 miles from San Bernardino, CA
- Price per square foot: $332 to $543 including design, installation, tax, and site work
- Construction and installation time: 3 months for construction, 2 to 4 months for installation
- Warranties: Not specified
Why It Made the Cut: Connect Homes allows home buyers to buck tradition with its ultra-modern designs. Folks who’d rather go a different route than a basic Cape Cod or ranch-style modular will want to consider Connect Homes. As one of the top modern modular home manufacturers, Connect offers truly modern designs that are clean, sleek, and efficient, making its models attractive to folks whose tastes don’t fit in a box. Pricing ranges between $332 to $543 per square foot and includes design, installation, tax, and site work. Connect Homes provides a streamlined collection of home floor plans, with 15 models available. While no two models are wildly different, sizes and shapes may vary to meet home buyers’ tastes. However, it can be difficult to compare these models side by side thanks to the company’s challenging web design. Luckily, the timeline for Connect Homes is about 5 to 7 months from the beginning of construction to installation, so time spent struggling on the website won’t be in vain.
Also Consider
Commodore Homes
Pros
- Comprehensive budget calculator tool
- Interactive online design tools
Cons
- No construction information available
- No pricing information available
- Service area: 35 states
- Price per square foot: Not specified
- Construction and installation time: Not specified
- Warranties: 1-year warranty on materials and workmanship; 10-year coverage for structural defects
Why It Made the Cut: With Commodore Homes’ affordable footprints and interactive design tools, home buyers can make sure they stretch their dollar as far as it will go without disappointment. Modular homes can be money savers, but some companies are more value-focused than others. Commodore Homes is one of the more budget-friendly options, allowing home buyers to manage their budget carefully. Commodore ensures the home buyer will know exactly what they’re getting into by providing a comprehensive budget calculator tool. This tool considers every factor, from site work to electrical hook-up, to help buyers know exactly what they can spend on a modular home. Construction lead time and pricing information is fairly limited, which could be a letdown for many home buyers. However, folks who want to design their own budget-minded home can use Commodore’s interactive online design tools.
Our Verdict
Folks looking for affordability, options, and speed will want to consider Clayton Homes. With its fast build times and award-winning building processes, it grabbed our top spot. For those who prioritize sustainable and environmentally conscious building practices, though, Deltec Homes is another great contender.
How We Chose the Best Modular Home Manufacturers
A lot of energy went into putting together this list of the best modular home manufacturers. We had to draw upon all our construction experience and industry knowledge to pick out the most important attributes for a manufacturer to possess.
Once we knew what to look for, we performed extensive research to find companies that met our criteria. We then compared them based on customizability, price, and speed to ensure that each manufacturer we suggested provided enough value. Those that failed our research and scrutiny were tossed aside, and those that passed were given awards based on their strengths.
Before You Buy From One of the Best Modular Home Manufacturers
The price of the actual home itself is only a slice of the pie, and it can be misleading. Site work, including excavation, foundation installation, utilities, wells, and septic systems, can easily surpass $100,000. Also, home buyers will want to factor in the price of the land. States such as Wyoming and New Mexico have some of the lowest land values, around $1,500 to $2,000 per acre. New Jersey has the highest land value in the country—over $196,000 per acre.
Most modular homes have some degree of customizability, but there’s at least one wall on each floor that isn’t customizable: the marriage wall. The marriage wall typically runs down the center of the home, parallel to the roof ridge, and it’s where the sections of the home meet upon delivery. Not only is this wall load-bearing, but it literally keeps the sides of the home together. It’s best to avoid modifying it without an engineer’s expertise.
Eighty to 90 percent of a modular home is completed in the factory, leaving 10 to 20 percent left for the site crew. Once the sections of the home are installed and married together, the homeowner can choose to finish the work themselves (as long as the lender agrees). Many folks opt to have the bottom floor finished by the crew and leave the upstairs unfinished, allowing them to save some money with sweat equity.
Cost of Buying From One of the Best Modular Home Manufacturers
The cost of buying a home from one of the best modular home manufacturers varies. However, the average ranges between $100 and $200 per square foot including installation, with high-end modular home manufacturers charging more. It typically costs between $72,000 and $144,000 to build an 1,800-square-foot modular home. Depending on the manufacturer, this may even include the cost of sending its crew to finish the project, though that’s often an extra expense.
Site work can cost much more, and manufacturers can’t provide a baseline price. Factors like rock ledges underneath the building site, poor drainage, and other obstacles can significantly affect the cost of installation and buttoning up. These additional expenses, including freight, land preparation, foundation, installation, utility construction, taxes, permit fees, and any additions like decks or garages, can cost between $51,000 and $167,000. This brings the total cost for an 1,800-square-foot modular home to between $123,500 and $311,000.
For these reasons, site work often becomes the biggest unknown variable in the construction project. Home buyers will want to leave room in the budget to account for these potentially hidden costs.
The Advantages of Using One of the Best Modular Home Manufacturers
Material and labor shortages can punt deadlines down the field. The biggest modular home manufacturers generally have a handle on any shortages, ordering large quantities of materials ahead of time. While modular home buyers won’t be totally protected from any delays, there may be a better chance of staying on track when going with one of the top modular home manufacturers.
Modular home manufacturers have a reputation for employee turnover, which could lead to inexperienced craftspeople building the homes. The best modular home manufacturers offer competitive wages and amiable working conditions, retaining staff for longer and promoting potentially better craftsmanship.
The best modular home manufacturers are typically more eco-friendly than stick-built constructors. The factory building process is highly efficient and minimizes waste as much as possible. Scraps from one stage of the project are typically recycled into another step down the line.
- There is more control over materials and labor shortages.
- Employee satisfaction and retention are typically better.
- The modular home process is highly efficient and minimizes waste.
FAQs
That might be a lot of information on the best modular home manufacturers, but there may still be some questions that need buttoning up. The following are some of the most frequently asked questions about these homes and the companies that build them.
Q. What is the difference between a mobile home and modular home?
The main difference between a mobile home and a modular home is that mobile homes are built on steel frames with wheels, while modular homes are designed for permanent foundations. Also, modular homes tend to be larger and consist of beefier framing members.
Q. How long do modular homes last?
Modular homes can last 100 years or more, or as long as a typical stick-built home.
Q. What is the difference between a prefab and a modular home?
Prefab is a term that describes any structure built in a controlled environment like a factory and then sent to its final location. Modular homes are simply one type of prefab home, which may also include manufactured or kit homes.
Q. Do modular homes depreciate?
Modular homes follow similar market trends as stick-built homes, unlike manufactured or mobile homes (which may not appreciate).
Q. Is it cheaper to build a house or buy a house?
It is typically less expensive to buy a home than it is to build one. However, shoppers can potentially save money by choosing a modular home.
Sources: HomeAdvisor, Flyhomes, Attainable Home