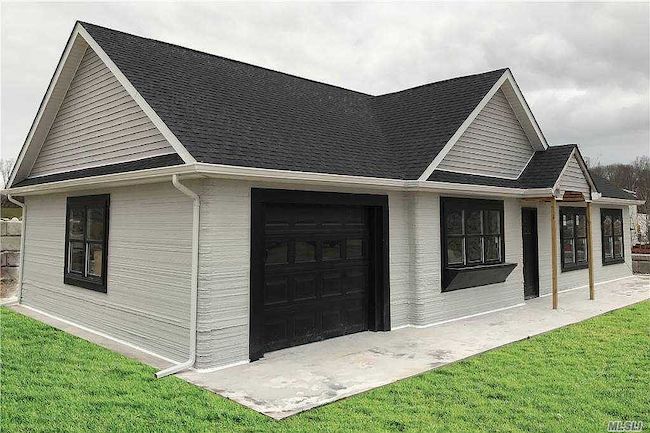
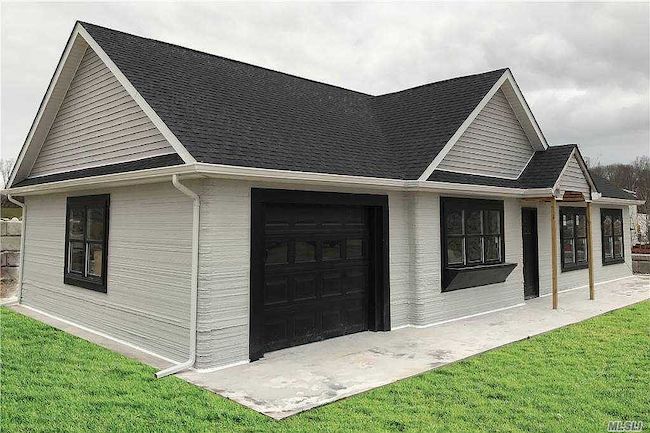
We may earn revenue from the products available on this page and participate in affiliate programs. Learn More ›
Three-dimensional printing isn’t just for little things—SQ4D, pronounced “S-squared,” a New York construction company, uses patent-pending 3D technology, known as Autonomous Robotic Construction System (ARCS), to print houses on-site. Now, the company’s first full-size spec house is on the market, and it looks a lot like a traditional house. Check out their 3-bedroom, 2-bath house in Riverhead, New York, and keep reading to find out more about this new type of construction.
How It Works
The basics behind printing 3D homes are nearly identical to those 3D printers use to create other items. Through the use of computer numerical control (CNC), a large concrete extrusion machine carefully follows paths designated for interior and exterior walls, depositing uniform layers of semi-solid concrete that cure to form a structurally sound frame. Each house is meticulously engineered to meet building codes. The company inputs a home’s architectural plans into its computer and then manually mixes and feeds concrete into the extrusion machine. The home in Riverhead took just 48 hours of concrete extrusion over eight days to complete the frame.
What’s Included
A 3D-printed house is comparable to other types of concrete-frame homes, including those built from precast concrete blocks and those where the exterior walls are formed and poured with wet concrete. But the finished home is not entirely 3D printed. The concrete extrusion machine creates the interior and exterior walls, and in some cases it may also form a foundation. For a close-up look at how the process works, check out this video from Apis Cor, a Utah-based 3D contractor.
Once the walls are complete, traditional framing takes over to build a truss or rafter roof system, add doors and windows, shingles, wiring, plumbing, and HVAC runs, and then complete the interior finish (cabinets, wallcovering, flooring, and fixtures) that make a house a home.

Cost Factor
Although it’s one of the most robust building materials around, concrete is also one of the least expensive, so the materials necessary to build a concrete house will be cheaper. The most significant savings, however, comes in reduced labor charges. For a traditional house, labor costs can range from 30 to 50 percent of the house’s overall cost.
According to Zillow, the SQ4D house in Riverhead is listed at $213 per square foot, which is about $60 to $70 cheaper than the per-square-foot price of comparable homes in the Riverhead community. Keep in mind that a lot of factors go into pricing a new home, such as the value of the lot it sits on, so the best way to understand a new home’s actual value is to chat with a local real estate agent who is knowledgeable about the houses in the community.
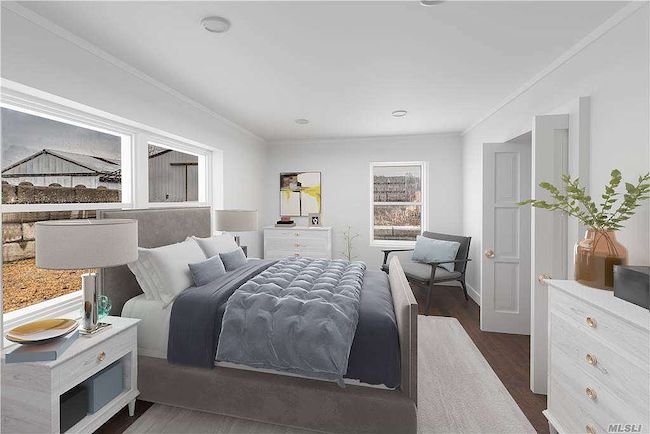
Environmental Impact
Framing a house in traditional style is a noisy, dusty endeavor that requires cutting down trees to harvest the wood necessary to frame the walls, floors, and roof. Right off the bat, a 3D-printed house is a more eco-friendly option because it saves trees. New concrete does off-gas as it cures; however, complete curing of concrete is 28 days. Once the concrete cures, the risk of off-gassing is minimal.
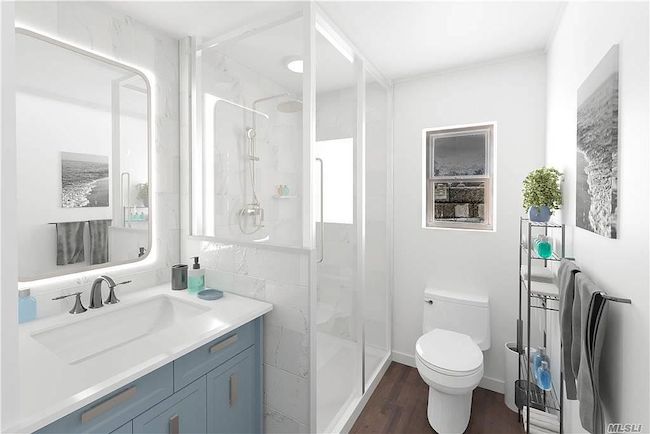
The Future of 3D-Printed Housing
As technology improves, it’s almost certain that 3D-printed structures will become more common. Currently, 3D printing is making it possible to create affordable homes for the homeless. According to The Architect’s Newspaper, an entire community of low-income housing, known as the Community First Village, has recently been developed in Austin, Texas, built by ICON, a robotics company. These homes offer something residents may not have had before—a safe place to call home. Three-dimensional printing won’t replace traditional construction anytime soon, but it offers an affordable and environmentally sound alternative.