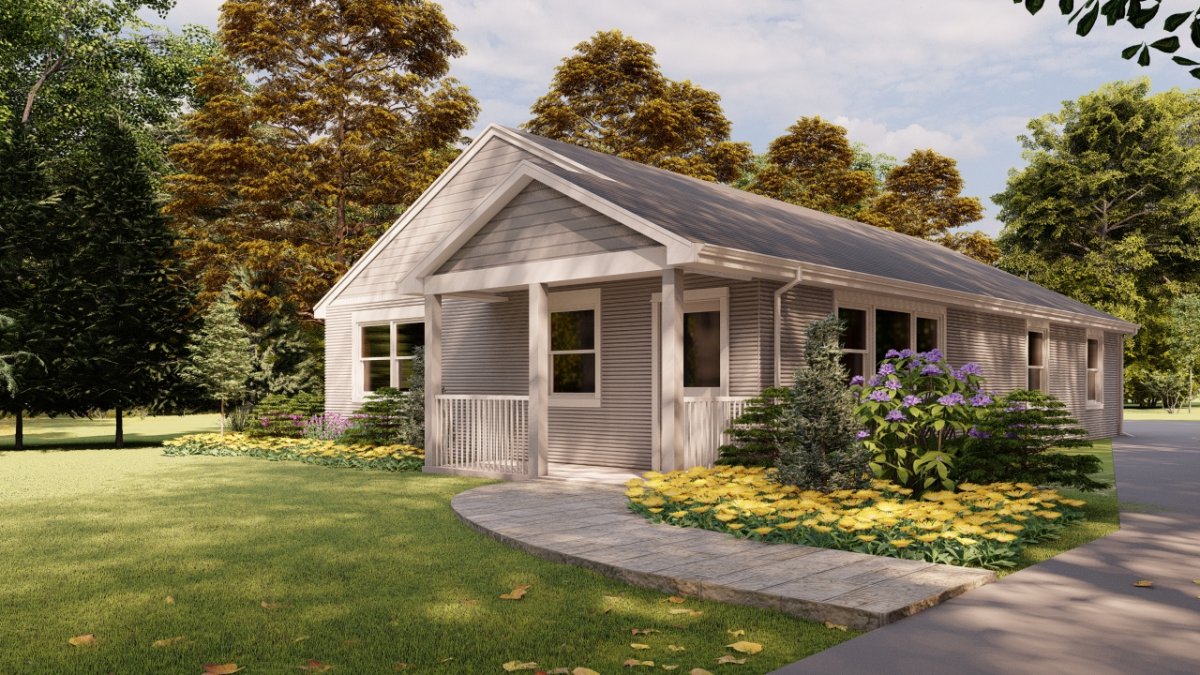
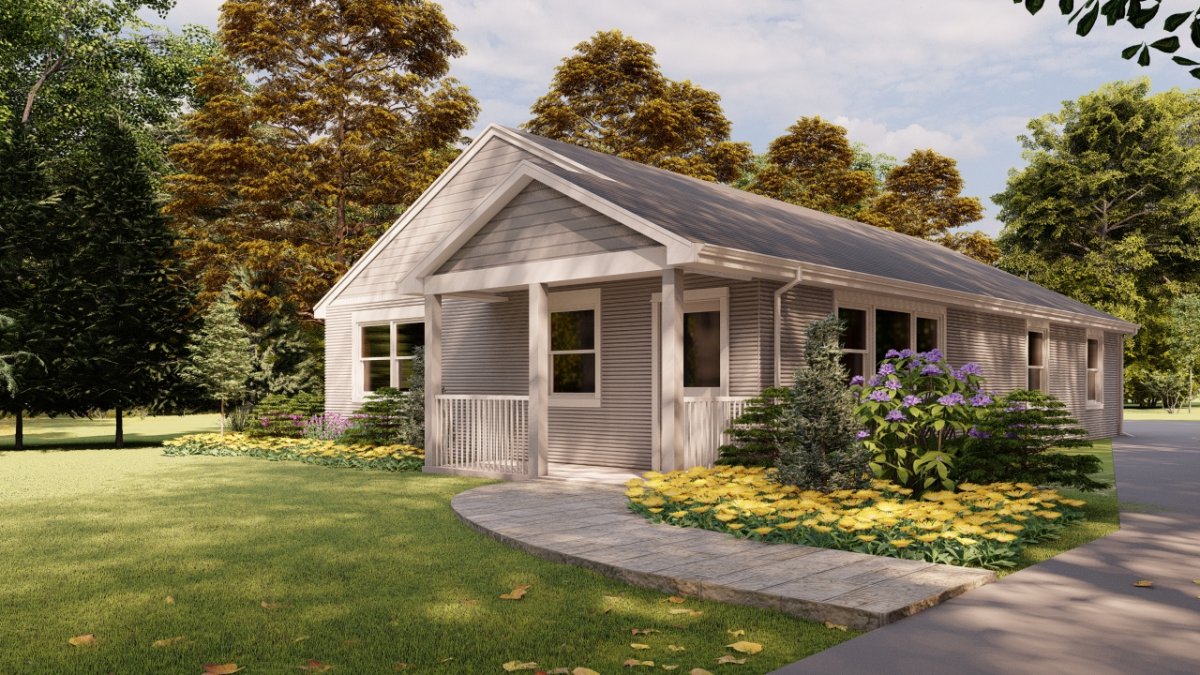
We may earn revenue from the products available on this page and participate in affiliate programs. Learn More ›
Recently, BobVila.com showcased a 3D-printed home in Riverhead, New York. Built by SQ4D, a New York construction company that specializes in 3D technology, the house is the first of its kind to land on the multi-list, but it’s unlikely to be the last. Kirk Andersen, director of operations for SQ4D, is looking forward to building many more 3D-printed homes. “The 3D-printing housing industry is only in its infancy,” Andersen says. His company is currently selecting the right buyer from multiple offers on the Riverhead house while planning additional computer-automated housing projects.
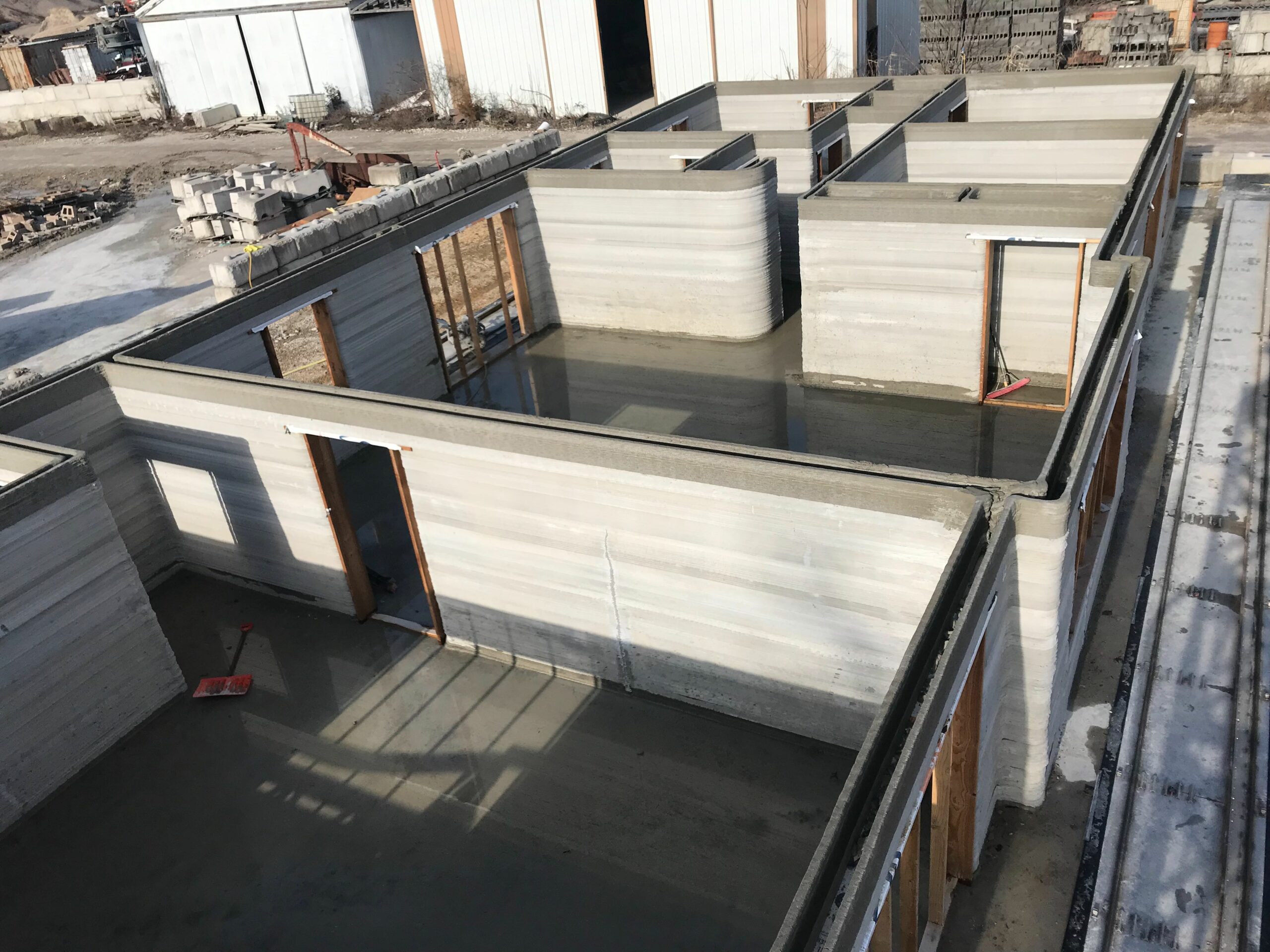
Affordable Housing
The cost to buy a home has skyrocketed in the past decade. According to the National Association of Home Builders (NAHB), as many as 75 million households will be financially unable to buy a median-priced home in 2021. To alleviate this situation, innovative companies are already figuring out ways to use 3D technology to create affordable housing. One such company, ICON, a construction technologies company based in Austin, Texas, is well on its way to making it possible for the financially disadvantaged to have homes of their own. In partnership with New Story, ICON recently completed a 3D-printed building project in Mexico that now provides safe, secure dwellings for families that could not afford traditional housing.
“The housing of our future must be different than the housing we have known,” says Jason Ballard, co-founder and CEO of ICON. “It’s time for a new paradigm… a paradigm that puts affordability, resiliency, beauty, comfort, and dignity in reach of everyone on this planet.”
While lumber and other building materials are at record prices, concrete, a staple in 3D home printing, is inexpensive, and its use can substantially reduce the cost of constructing a home.
Sustainability
Harvesting the lumber required to build traditional homes contributes to deforestation and a loss of biodiversity, ecological ills that SQ4D is eager to help avoid. All that’s needed to print the concrete structure of a 3D home is “Portland cement, sand, and water,” Andersen says. Being able to build affordable homes and protect the environment at the same time is a major goal of both SQ4D and ICON.
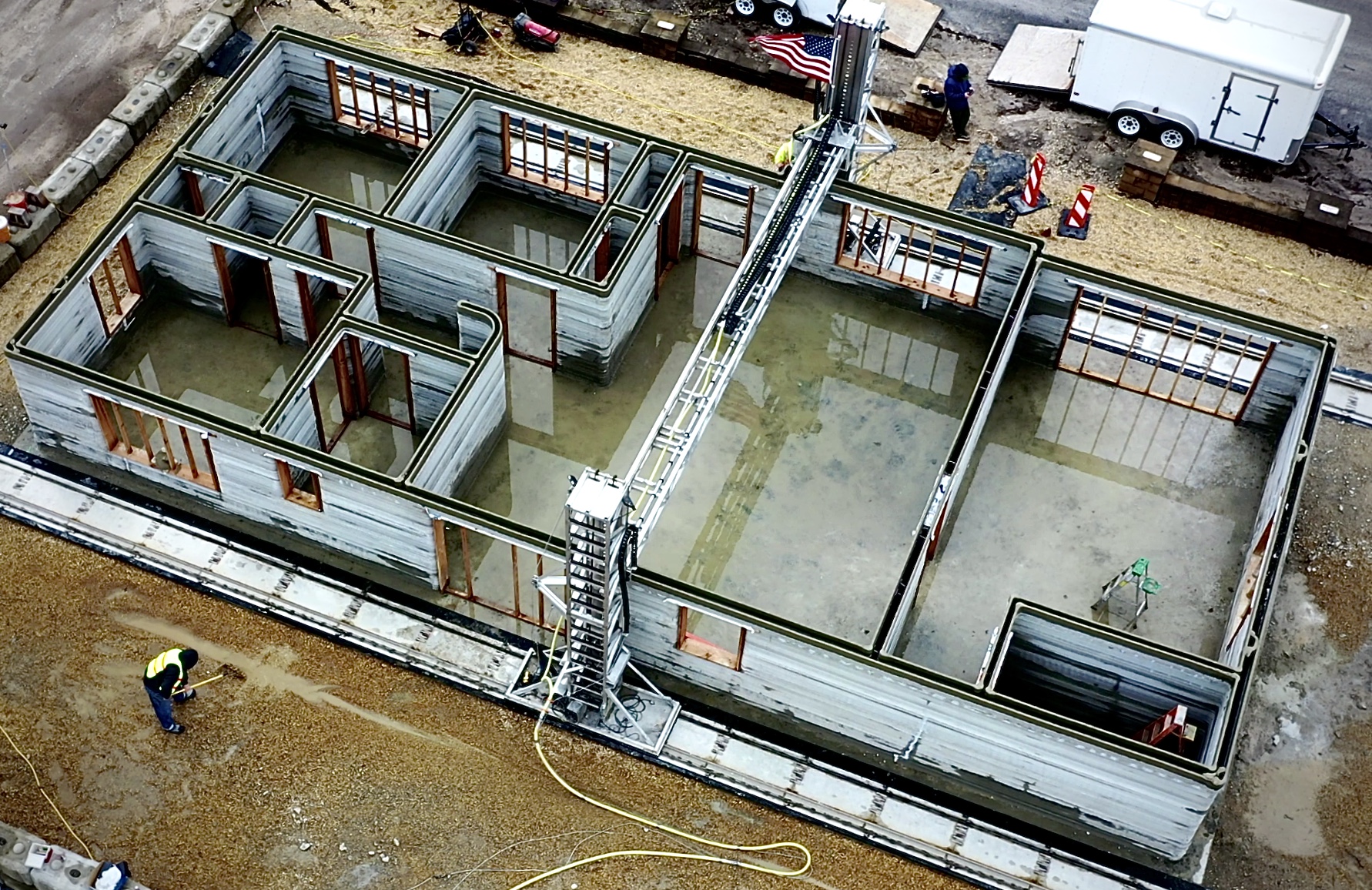
Traditional Building Trades
While tried and true, the traditional building process—pouring a foundation, stick-framing walls, and then setting roof rafters before adding the rest of the home’s elements—requires a lot of physical labor. It’s easy to understand why traditional contractors may be concerned about losing construction jobs to automated technologies.
Is there any place in the 3D-printed equation for carpenters, roofers, and mechanical trades such as plumbers and electricians? “Yes,” says Brooke Bauguess, VP, Communications & Public Affairs at ICON. “Once we deliver the full wall system with the Vulcan construction system, the other building trades come in to put on the roof and install the windows, doors, and the rest of the house.”
Carpet layers, painters, cabinetmakers, and many other construction trades will still have a place in creating new homes. However, one of the more dangerous residential construction phases—building the frame of a house—will be completed using computer-automated construction.
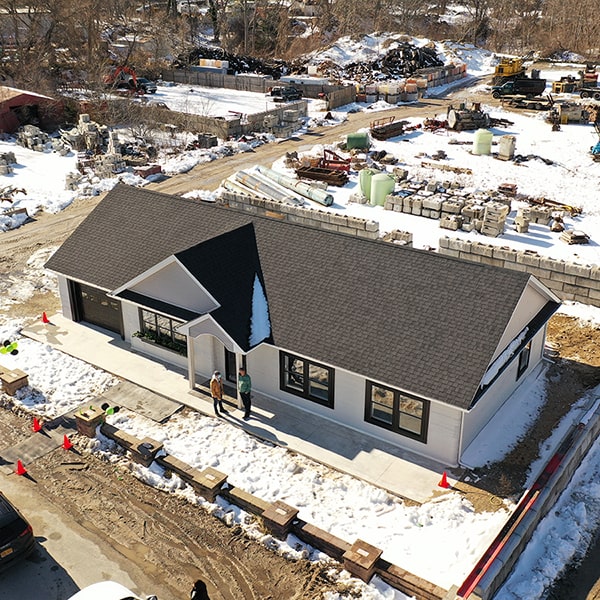
Full Speed Ahead
With interest in 3D-printed construction growing rapidly, both SQ4D and ICON stand ready to increase production. Some snags still exist—for instance, local building codes can present obstacles—but Andersen believes codes will eventually be revised to support 3D construction once inspectors realize 3D printing creates a more robust and safer house. Meanwhile, the technology has not gone unnoticed by scientists and forward-thinking researchers. Having received funding from NASA, ICON is looking to develop a space-based construction system that could help researchers further explore the moon.
While 3D-printed homes are still rare, the technology is quickly proving to be a cost-effective way to build durable homes and other structures. Not only is 3D printing fast and efficient, but computer-aided software can also adapt a design to suit an individual homeowner’s preferences, increasing versatility and opening the door to a whole new world of affordable, stylish housing. Andersen predicts this is just the tip of the iceberg and that 3D-printed houses will one day become commonplace.