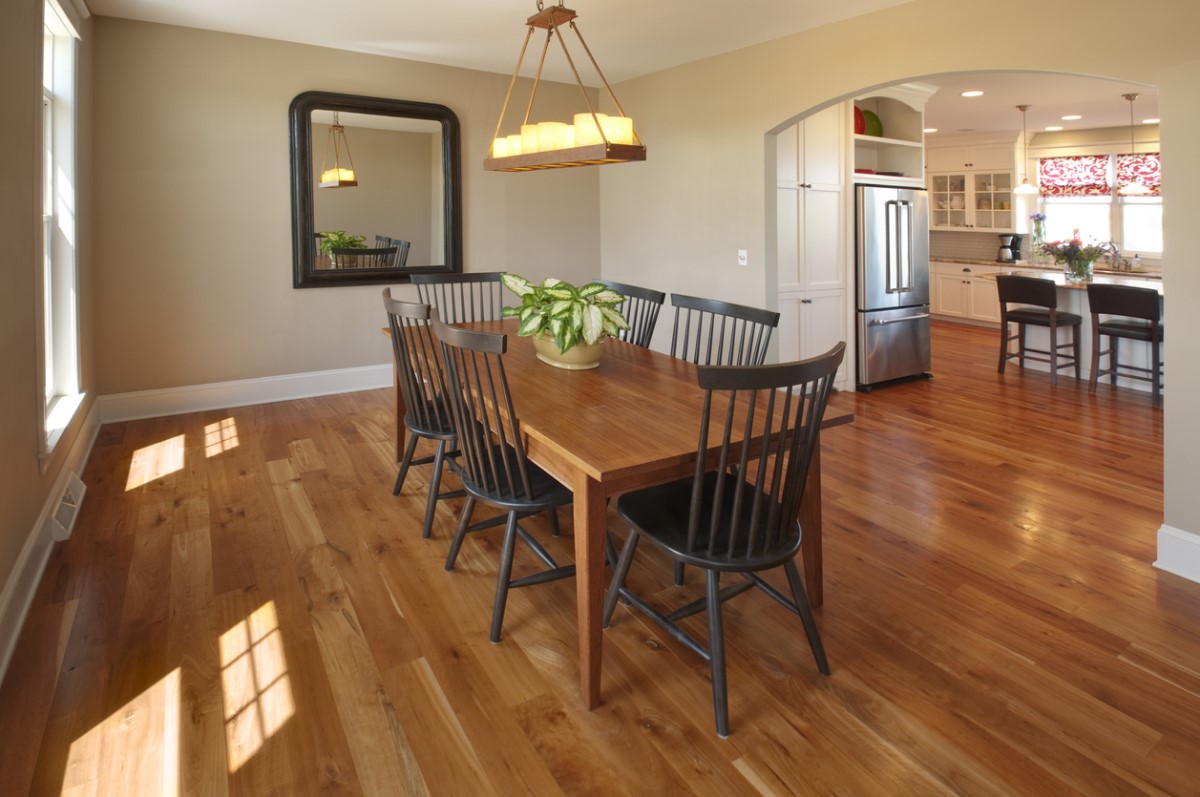
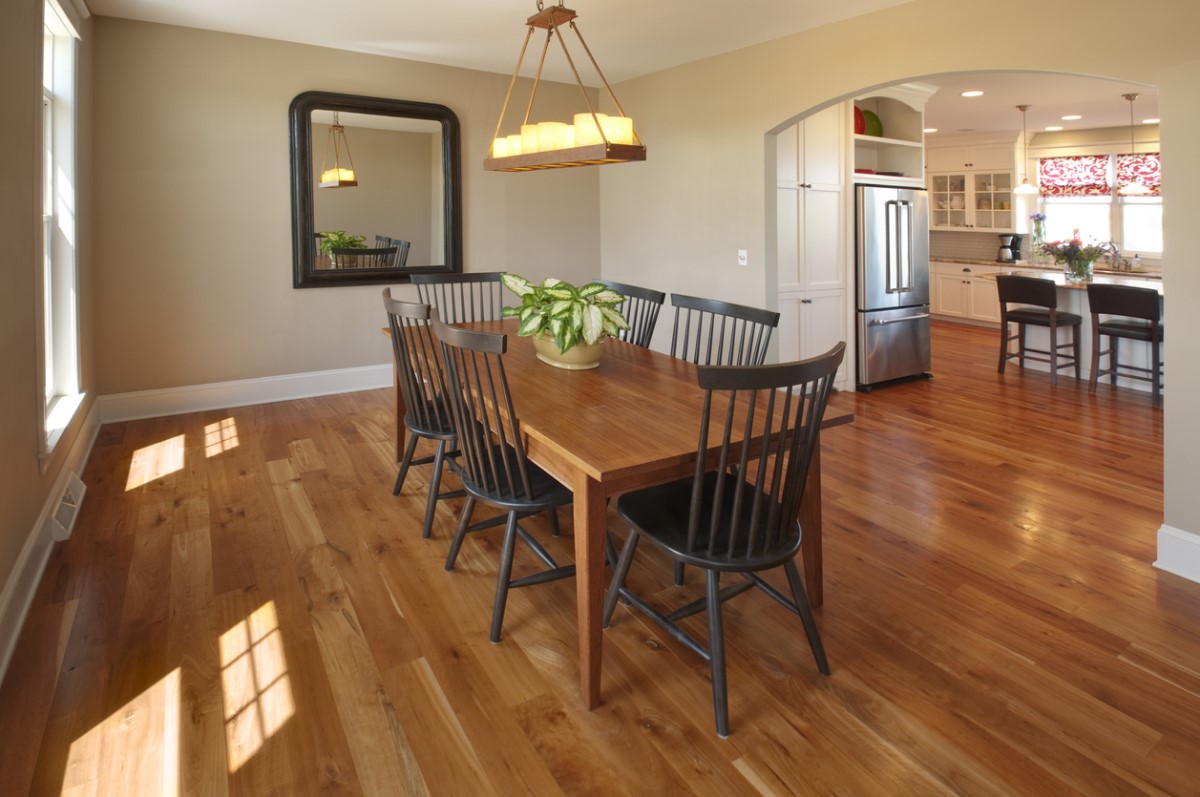
We may earn revenue from the products available on this page and participate in affiliate programs. Learn More ›
Hardwood floors add natural warmth to any room, but the traditional method of installing hardwood is time consuming and messy, and it exposes the installer to toxic fumes from stains and sealants. It’s no wonder that even experienced DIYers often opt to hire a pro for the job! Prefinished hardwood flooring, which are hardwood planks that are sold with stain and sealant already applied, offers an easier alternative for achieving the beauty of a real wood floor. Like all flooring materials, however, prefinished hardwood flooring has its advantages and disadvantages. Read on to learn about its benefits and drawbacks before deciding if it’s the right material for your home.
Prefinished wood flooring offers a more durable finish than traditional hardwood flooring.
Durability is one of the most notable differences when comparing prefinished hardwood to unfinished hardwood flooring. During manufacturing, prefinished hardwood floors are treated with an aluminum oxide crystal sealant—one of the best hardwood floor finishes for an extremely rugged surface that can withstand heavy foot traffic, moving furniture, and other forms of wear and tear. In contrast, traditional hardwood floors are first nailed into place and then stained and sealed. Because neither DIYers nor flooring contractors have access to manufacturer-grade sealants, traditional hardwood floors aren’t as durable as their prefinished counterparts and can begin to show scratches and surface dulling in as few as 5 to 7 years. Prefinished flooring coated with superior chemical sealers can maintain its good looks for as long as 25 years without dulling or wearing thin.
RELATED: What’s the Difference? Prefinished vs. Unfinished Hardwood Flooring
Fewer design options are available with prefinished flooring products.
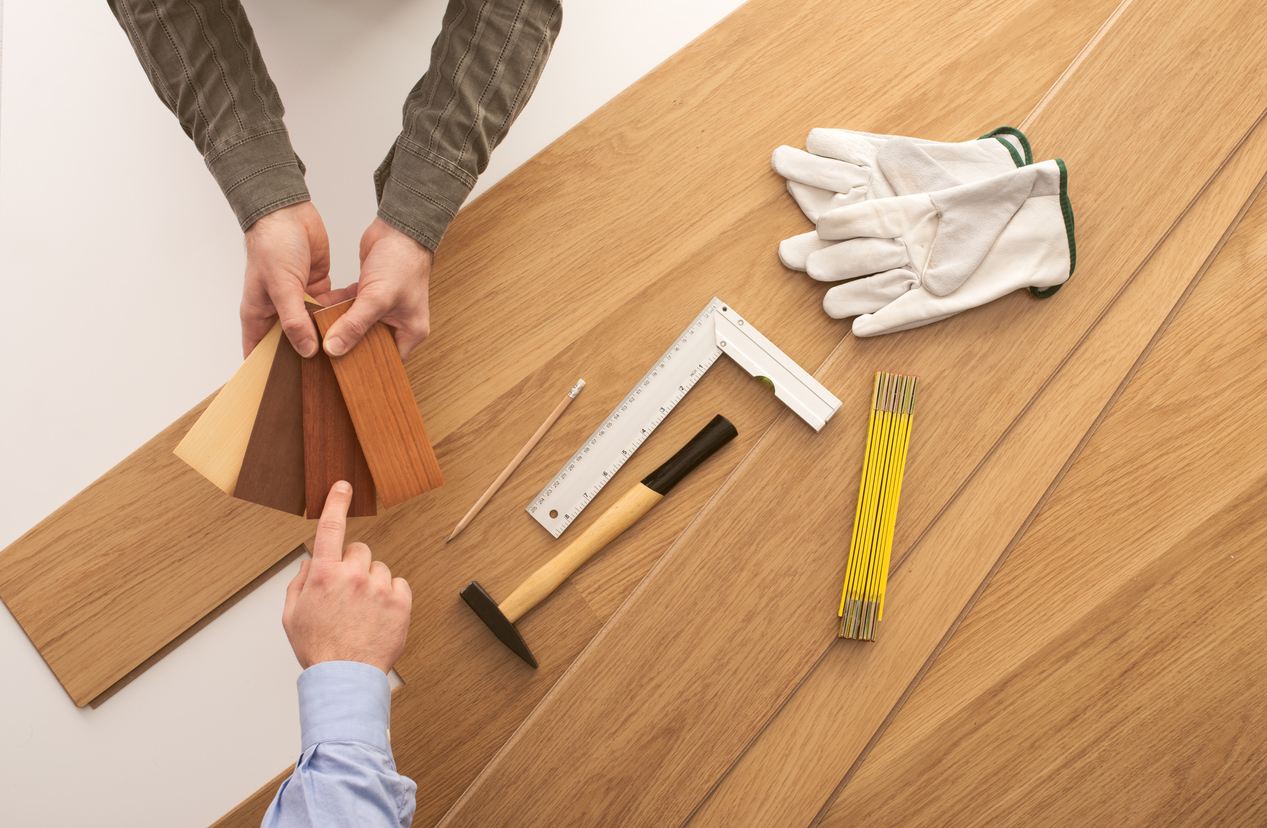
In the traditional hardwood floor selection process, you can choose from dozens of wood species and then select from dozens more stain and sealant options. This allows you to get the exact wood grain look, color, and surface sheen you want. Not so with prefinished hardwood, which comes in a limited variety of wood types (such as red oak and maple), colors, and sealants.
The installation of prefinished wood flooring is quick.
There’s no denying the simplicity and speed of installing a prefinished wood product, which is a boon for homeowners who are staying in the house during a renovation. You can easily learn how to install a prefinished hardwood floor online and then do it yourself. Installing a traditional wood floor, on the other hand, can take 2 weeks or longer because the project is completed in phases: installation of the planks, sanding the surface, staining the hardwood floors, and then applying two or more coats of a sealant that may need days to cure. Not only is the process lengthy, but it’s also messy and can produce toxic fumes. With prefinished flooring, there’s no downtime—as soon as the planks are installed, you can walk on the floor and start arranging your furniture.
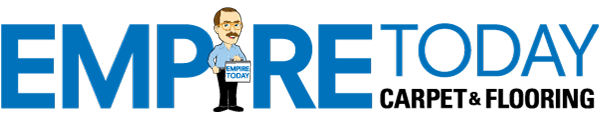
Carpet, hardwood, tile, vinyl, and laminate flooring.
Bob Vila has partnered with Empire Today® to help you easily get beautiful new floors at a great price.
Free In-Home Estimates
Subfloor irregularities can show through prefinished hardwood floors.
When installed on a level subfloor that has no dips or heaves, prefinished hardwood flooring will look just as smooth as a traditional hardwood floor. But unlike traditional flooring that can be sanded to remove lippage (slight inconsistencies in floor level where planks abut), prefinished planks cannot be sanded because the boards are already finished. If the subfloor is uneven in spots, it could cause some of the planks to raise slightly or result in visible gaps between the planks. The effect is not usually very noticeable, but it could be if the subfloor is seriously uneven.
Prefinished hardwood flooring has visible seams.
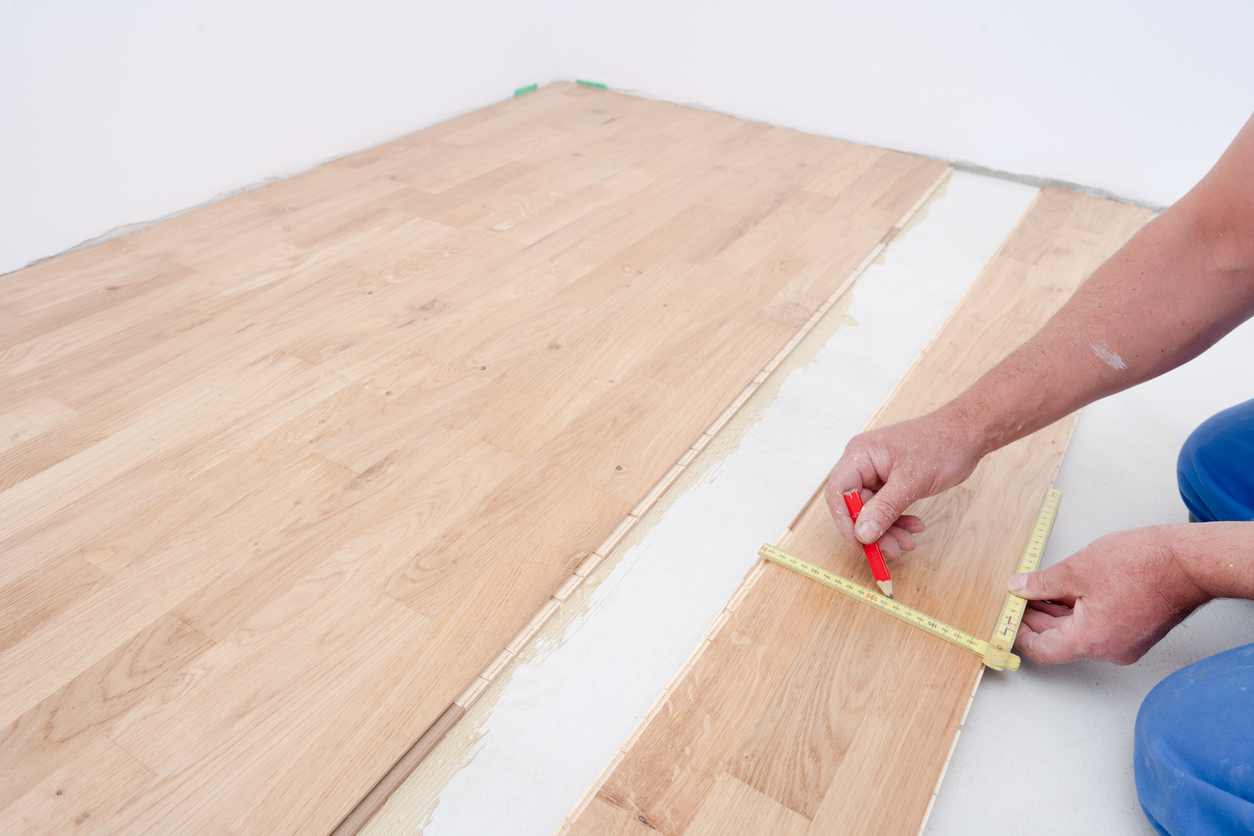
In order to give the tops of planks a smooth finish, the manufacturer creates bevels along the top edges of each plank that are called cambers. These bevels are very small, just a tiny fraction of an inch, but when two planks are installed side by side, the bevels create a shallow “V” groove along every seam, creating visible lines. While some people like the look of the grooves, others prefer the perfectly flush look of traditionally finished hardwood flooring that has been sanded smooth. The grooves sometimes also serve as a spot for dust and debris to collect, making prefinished floors slightly harder to keep clean.
Prefinished hardwood planks can be refinished, just as traditional planks can.
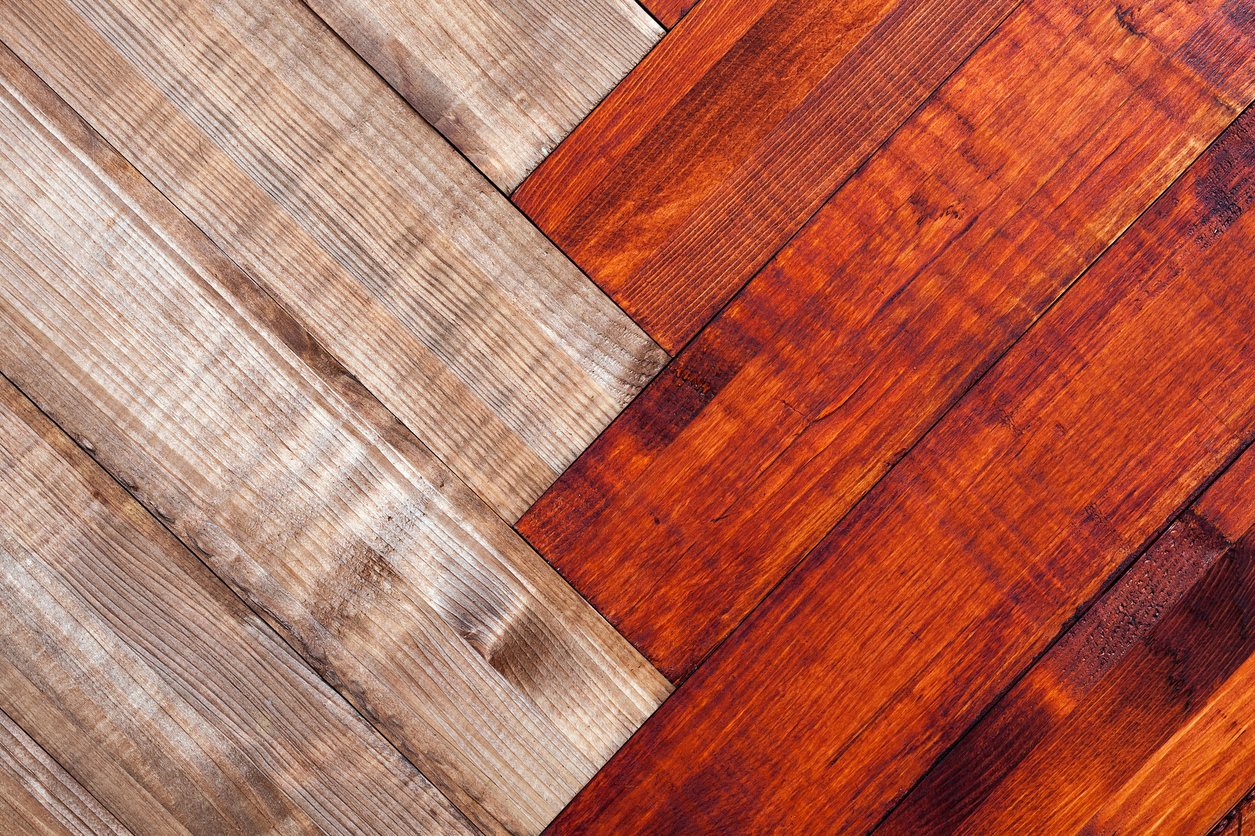
Install prefinished hardwood and it will look new for decades. But if down the road you decide you’d like to change the stain of your finished wood planks, you can do so. A prefinished hardwood floor is still solid, real wood flooring, after all, so the surface can be sanded and a new stain and sealer applied, just as with a traditionally finished wood floor. Sanding the finish usually takes a little longer than it would with a traditional wood floor, however, because the sealant is harder.
Including installation, the cost of prefinished hardwood flooring is about the same as traditional hardwood flooring.
While the cost to install prefinished hardwood floors is much less than the cost to install traditional hardwood floors, the prefinished planks themselves are pricier than traditional unfinished wood planks. What you’ll save in labor you’ll most likely spend in the higher cost of the prefinished planks. Expect to pay between $5 and $10 per square foot, depending on the type of wood and quality of the finish, to have prefinished wood flooring professionally installed.
Installing prefinished hardwood planks is easier to DIY.
If you’re planning to install your own hardwood floor, prefinished is by far the easier process. You’ll still have to nail each plank to the subfloor individually, but there’s no messy sanding. There’s no need to get the room dust-free, either, which you would otherwise need to do before staining and sealing. Likewise, when installing prefinished hardwood flooring you won’t have to worry about inhaling harsh fumes from stains and sealants. If you opt to DIY your flooring installation, you can save $2 to $5 per square foot over the cost of professional installation.
Prefinished hardwood plank flooring requires less ongoing maintenance than finished hardwood flooring.
Factory-finished hardwood planks can be treated with a more durable finish than can be applied on-site. This means you’re less likely to have to sand and refinish prefinished hardwood flooring at regular intervals; you may, in fact, have as many as 25 years before an overhaul is required. With hardwoods finished on-site, however, you’re looking at as few as 5 years between resurfacing treatments.
One might argue that the “grooves” in prefinished flooring require a bit more attention to detail in terms of routine cleaning, but a broom or vacuum generally picks up debris from the indentations just as it does from the surface of the floor.
When selecting the right prefinished hardwood for your flooring, consider these other factors.
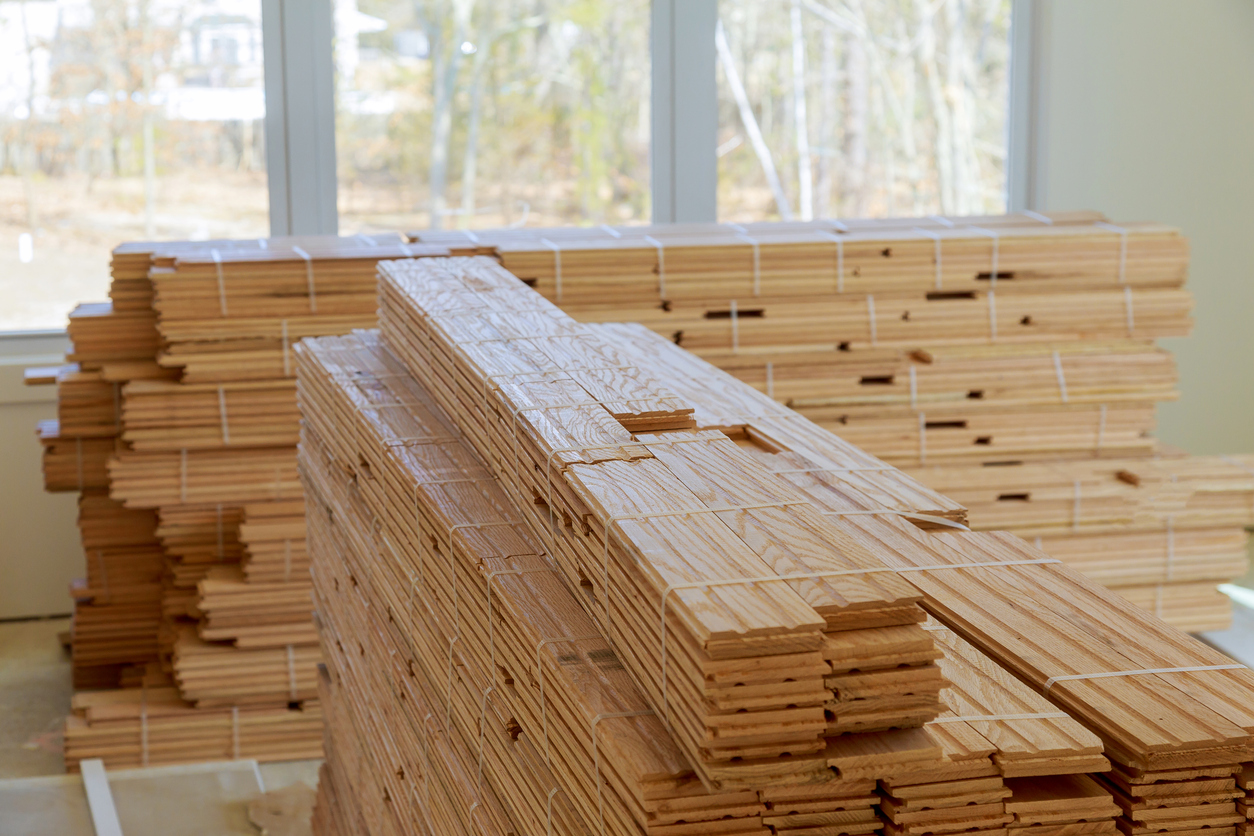
Should you decide prefinished hardwood is the right choice for your home, the following tips will help you choose the best planks for your project.
- Engineered hardwood isn’t prefinished hardwood. When shopping for prefinished hardwood, you’ll likely come across a selection of what’s called “engineered hardwood.” These products are not real hardwood but are instead manufactured laminate planks with a thin layer of hardwood on the surface. While these offer the look and feel of hardwood, they are actually “floating floors” that do not attach to the subfloor. While engineered hardwood floors can be lovely, most cannot be refinished, and the finish on the cheaper varieties is often thin and dulls quickly. To make an informed choice, learn more about different types of hardwood flooring.
- Narrow planks take longer to install. The largest selection of prefinished hardwood planks comes in widths from 3 inches to 4¾ inches. These plank sizes offer a classic look that flatters many home designs. Keep in mind, however, that the narrower the planks, the longer it will take to install the floor—and if you’re hiring a pro, you’ll pay more in labor.
- Wide planks suit large rooms. Prefinished hardwood planks that are more than 4¾ inches wide are popular for their rustic country appeal. But wider planks tend to make rooms look smaller, so this width is best suited to spacious rooms.
- Consider how much traffic the room gets when choosing a wood species. Hardwood is rated on the Janka scale, named for Gabriel Janka, who developed the rating system. The higher the number, the harder the wood. The standard hardness for wood flooring is around 1,290, which corresponds to one of the most popular flooring species, red oak. If you have active kids or pets, however, you may want to choose a harder type of wood, such as white oak, which has a Janka rating of 1,360.
Final Thoughts
When it comes down to making a final decision about whether prefinished hardwood flooring is right for your home, ask yourself three important questions.
How much time do you have? If you’re unwilling or unable to wait the many days it takes for the in-place finishing process, prefinished might be the better option.
Do you prefer the flat, unbeveled look of traditional hardwood flooring? If so, go with that and avoid prefinished flooring, which has a bevel along the top edges.
Finally, how much care and maintenance are you prepared to give your floors? Because the sealants that are applied at the factory tend to be more durable than those that can be applied on-site, prefinished hardwood flooring generally requires less maintenance.
FAQs About Prefinished Hardwood Floors
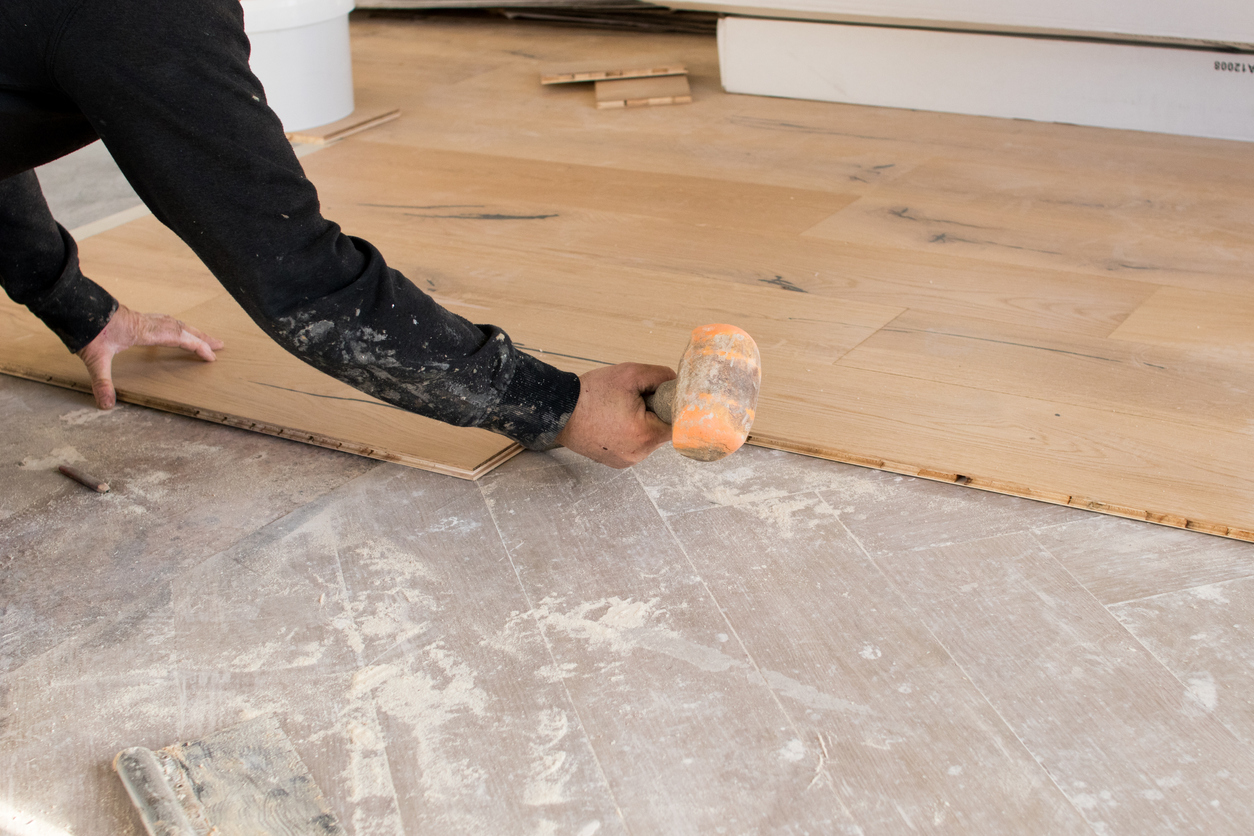
Do you need additional clarity on the topic of prefinished hardwood floors before you make a decision? Check out the answers to these frequently asked questions to get the information you need.
Q: How long do prefinished hardwood floors last?
Hardwood floors, whether prefinished or not, are undeniably long-lasting. The finish on these floors will need to be reapplied, however, to keep the wood protected and looking great. The factory finish on prefinished flooring can last as long as 25 years before it needs to be refreshed.
Q: Can prefinished floors be refinished?
Prefinished hardwood floors can indeed be refinished. Because the coatings are so durable, removing them can be arduous, but it can be done. Once the old finish has been removed, a new one can be applied.
Q: Do you need to seal prefinished hardwood floors?
Most prefinished hardwood floors come fully sealed from the manufacturer and require no additional sealing. In fact, adding extra sealant can damage or destroy the factory-applied protectants. Having said this, it’s a good idea to double-check the manufacturer’s instructions for your particular flooring to ensure that no additional sealant is required, or to find out what type is recommended if you really feel the need.