-
Lawn & Garden
Bob Vila’s 10 “Must Do” Projects for April
-
Lawn & Garden
9 Ways to Thwart Nosy Neighbors and Protect Your Privacy
Hi, I'm Bob Vila
You probably know me from TV. For the better part of a half century, as the host of shows like This Old House and Home Again with Bob Vila, I’ve been teaching and inspiring people to upgrade their homes and improve their lives. I learned firsthand about home building from my father, and I’ve written more than a dozen books about remodeling, buying your dream home, and visiting historic homes across America. It’s fair to say that buildings, especially homes, are my life’s work.
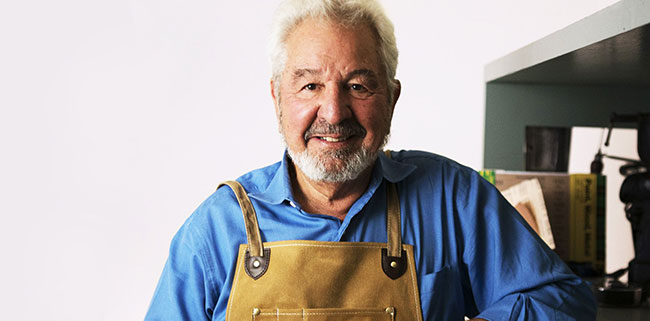
Lawn & Garden
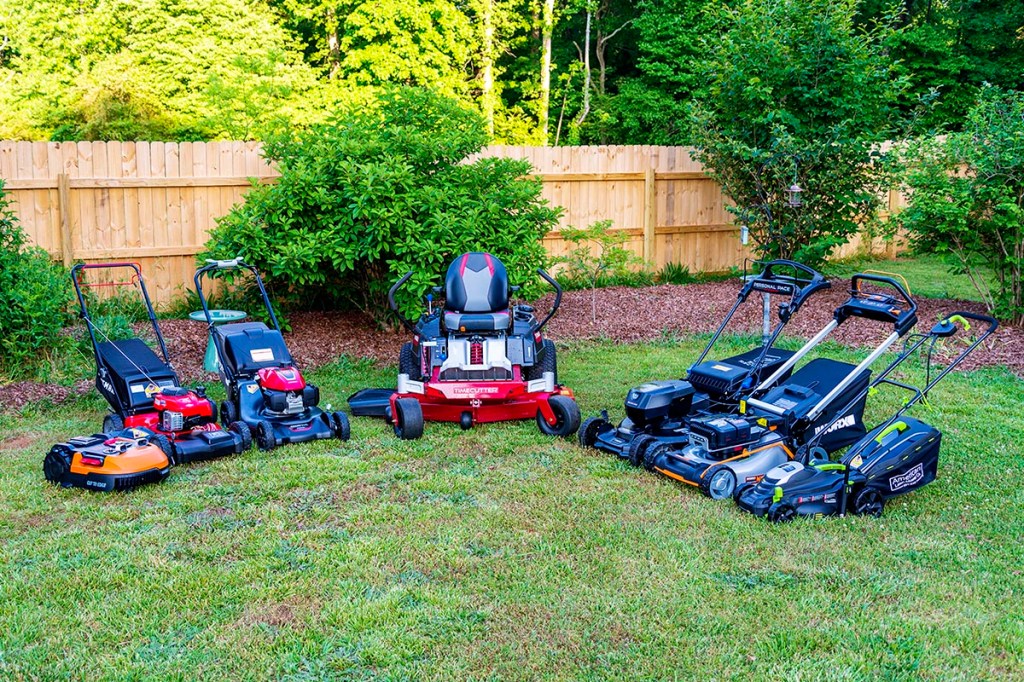
The Best Lawn Mowers Tested in 2024
Make your yard the envy of your neighbors with one of these top lawn mowers.
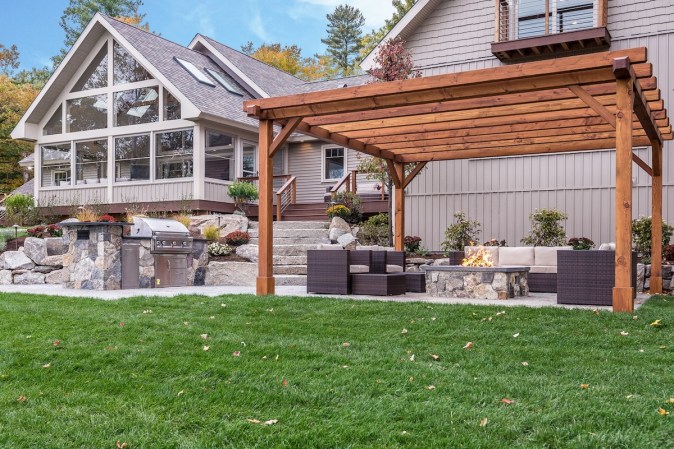
What Is Hardscape, Anyway?
DIY
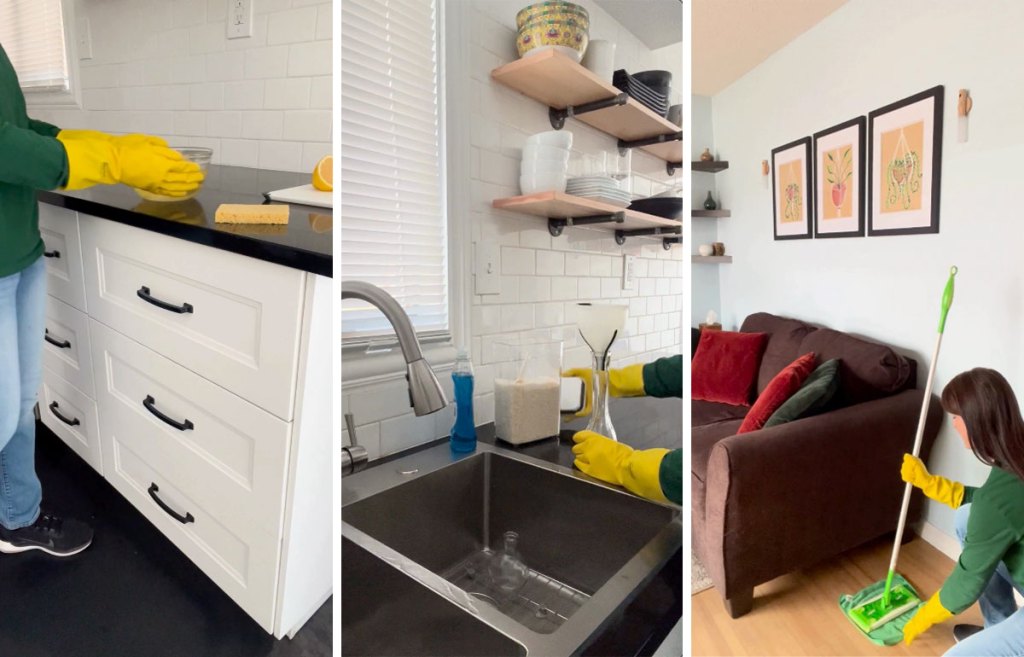
I Tried 3 Spring Cleaning Tricks—and I’ll Be Using Them From Now On
You’ll want to keep these up your sleeve, too.
By: Jenny Stanley
How we test and review products
The Bob Vila Product Reviews team tirelessly researches and tests products to ensure they live up to the hype.
- Our team scours the market for best-in-class products.
- We do our homework and thoroughly vet popular products.
- We’ll test as many as we can get our hands on.
- Our unfiltered, honest opinion is what you see on the page.
-
Appliances & Cookware
The Best Vacuums to Keep Your Apartment Clean and Tidy, Tested
-
Cleaning & Organizing
9 Tools the Bob Vila Team Swears By for Spring Cleaning
Curb Appeal

10 Ways You’re Killing Your Curb Appeal
Never underestimate the importance of curb appeal. Not only does your home exterior give a first impression to guests, it can also influence real estate transactions by attracting potential buyers. Unfortunately, though, some common eyesores can leave your facade looking worn for wear. Check out these 10 mistakes that are killing your home’s curb appeal, and learn how to banish the blemishes for a picture-perfect landscape.
By: Cody Calamaio
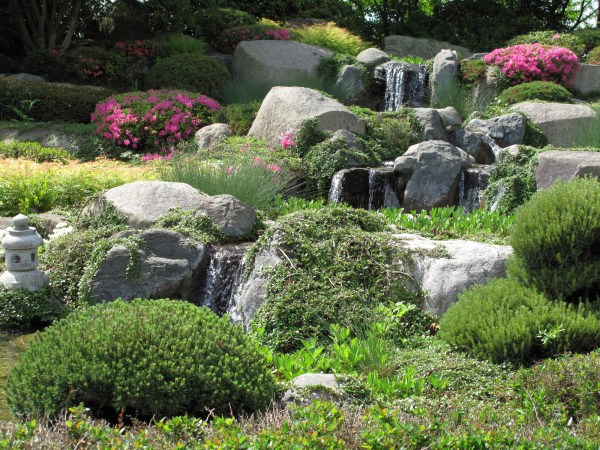
15 Gorgeous Rock Garden Ideas for Your Landscape
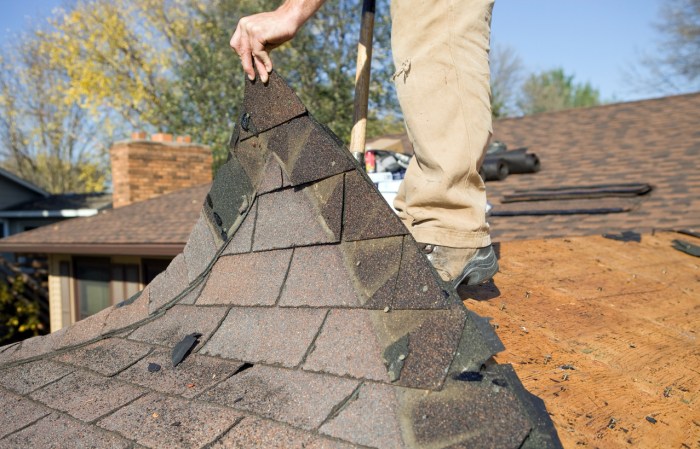
How Much Does Roof Replacement Cost in 2024?
Meet the Experts
We’re not just here to answer your questions and offer advice. BobVila.com seeks to educate and empower.
Our team of writers and editors are passionate about all things home. We are general contractors, master gardeners, real estate pros, historic preservationists, product testing specialists, and veteran journalists with expertise in everything from design to DIY. Our common bond is the mission of BobVila.com—to simplify, demystify, and chronicle the joys and challenges of homeownership through a commitment to accuracy, clarity, accessibility and good old-fashioned fun.
BobVila.com is the complete toolbox and ultimate resource for inspirational ideas and nitty-gritty know-how. It’s been that way since the site began in 2011. Our goal is to carry forward Bob Vila’s decades-long tradition of helping people maintain and upgrade their homes to live better each day.