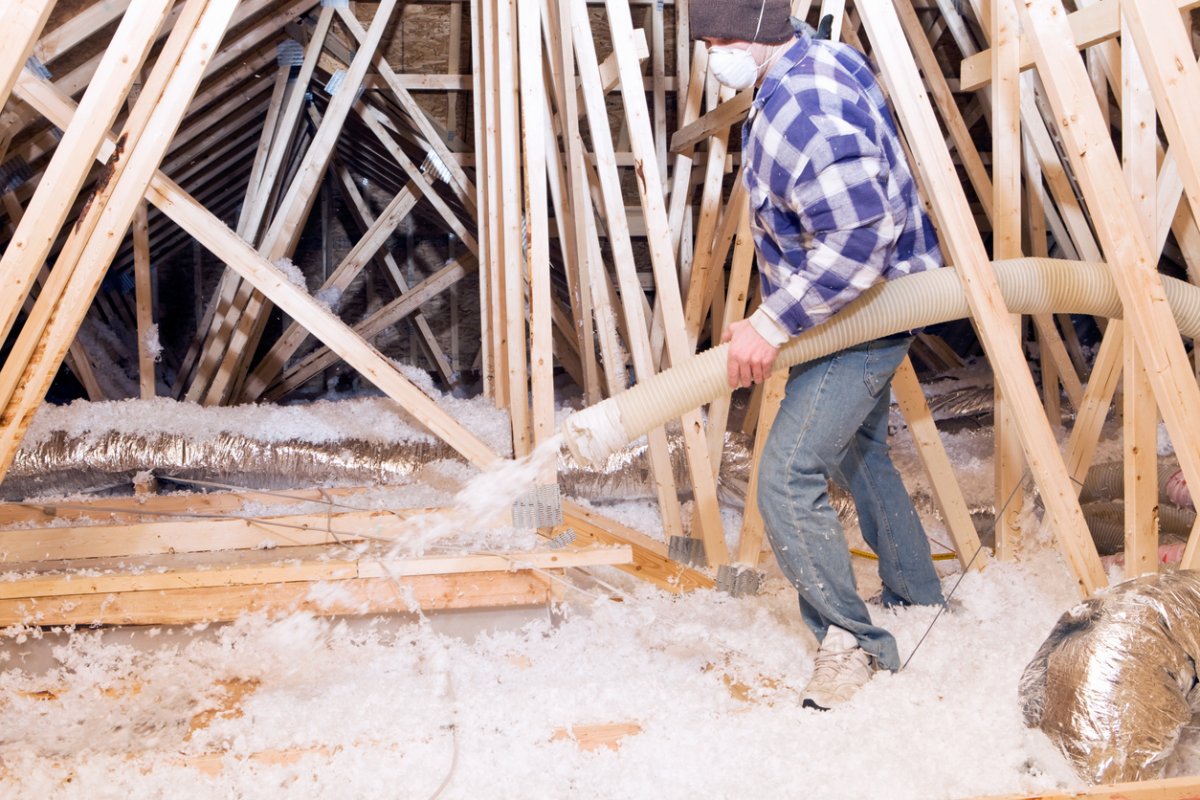
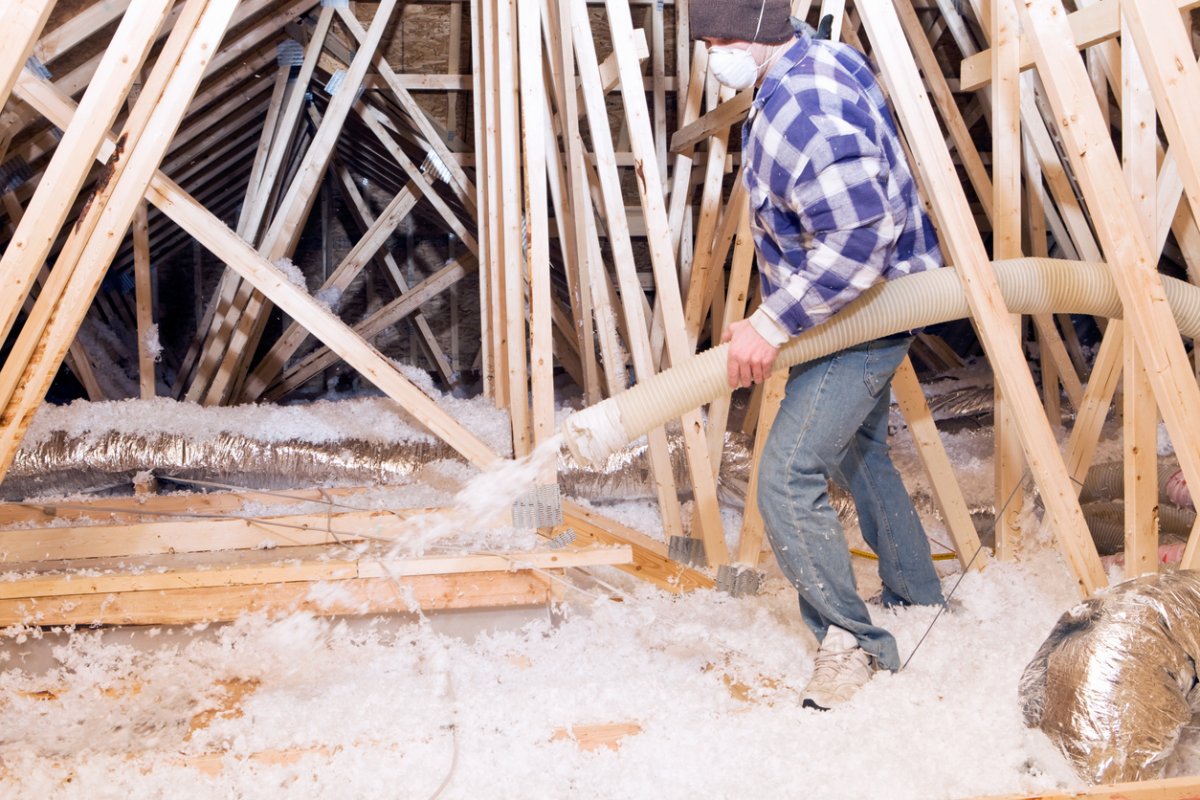
We may earn revenue from the products available on this page and participate in affiliate programs. Learn More ›
Wintry drafts snaking through an old house usually indicate that it needs insulation. Insulating your home is essential for warmth, energy efficiency, comfort, and indoor air quality. However, if an entire gut job—stripping the interior back to its studs—is not feasible, retrofit insulation is the next best option. While there are different types and techniques, aided and abetted by modern technology, marrying new types of insulation with an old home that’s been without it for its lifetime is not without its issues.
Contractor Jim Zazera of Jenza Renovations in Pittsburgh is a 40-year construction veteran and is extremely familiar with retrofitting insulation to fit Pittsburgh’s older housing stock, particularly recently during the city’s house flipping boom.
“Often in older homes, there’s a lot of high-quality interior finishes you want to keep, so it doesn’t make sense to go ripping open walls. If you are replacing the exterior siding, you can use blown-in or foam insulation from the outside by making holes at regular intervals,” he says. “You have to choose the right insulation for the job and what you intend to do with the home.”
Let’s dig deeper to find out which old house insulation options are right for you.
Blown-In Cellulose
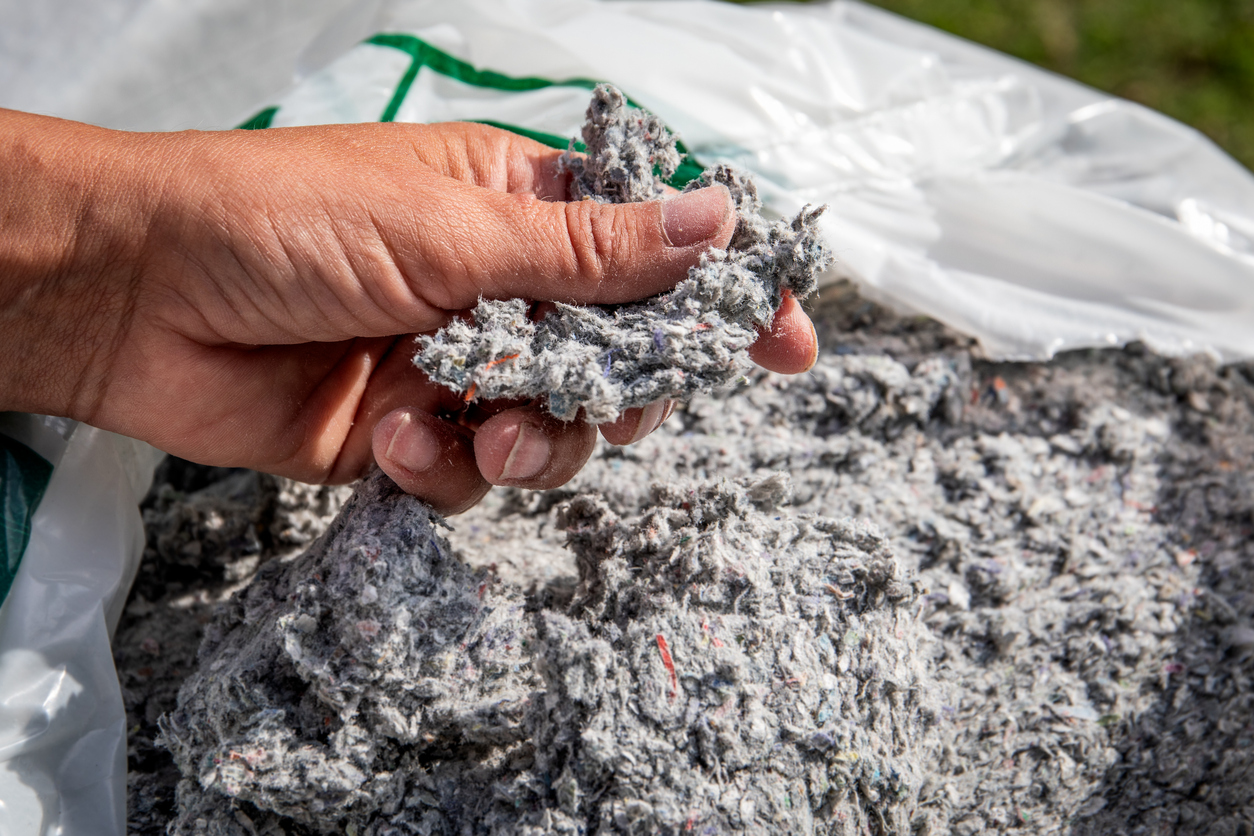
Pro: Conforms to awkward spaces.
Blown-in cellulose insulation is dense and clumpy. It’s also made up of thousands of pieces of recycled cellulose, which can fit in enclosed areas and conform to awkward spaces around pipes and ductwork. Installed using a machine and hose, it can fill hard-to-reach spaces of different sizes, providing a high R-value (thermal resistance). It is particularly good at reducing air leakage and noise transmission. For these reasons, it’s often used in older homes once the drywall has been removed.
Con: Becomes compact and uneven over time.
As it’s clumpy, blown-in cellulose can get compacted and settle over time, losing some of its effectiveness. Also, the installation process can get messy and dusty, requiring proper ventilation, masks, and eyewear. It can also be susceptible to mold or pest infestation depending on the material used.
Injection Foam

Pro: Targets hard-to-reach spaces.
Injection foam is an expanding foam insulation that—as the name suggests—is injected into existing wall cavities through small holes. It’s an obvious advantage for those who need to insulate tight, hard-to-get-to areas that would otherwise be difficult to reach without removing existing siding or drywall, keeping costs down. Injection foam is particularly good for filling a wall cavity very quickly with an airtight seal, improving the soundproofing.
Con: Requires a specialist to install.
It can be expensive when compared to other types of insulation, as installation requires a specialist. Also, if not applied uniformly, the expanding foam can exert nonuniform pressure on walls and windows, causing cracking or bulging. Using low-expansion foam can reduce this possibility. Because the insulation is exerted without visual oversight, it’s hard to judge the quality and coverage once installed.
“The liquid foam has increased in popularity, but one of the issues is that it encapsulates everything,” says Zazera. “So if you have pipes and other fixtures you may need to get to later, it’s probably not a great option. I’ve heard plumbers complaining about scraping it off pipes.”
Batts
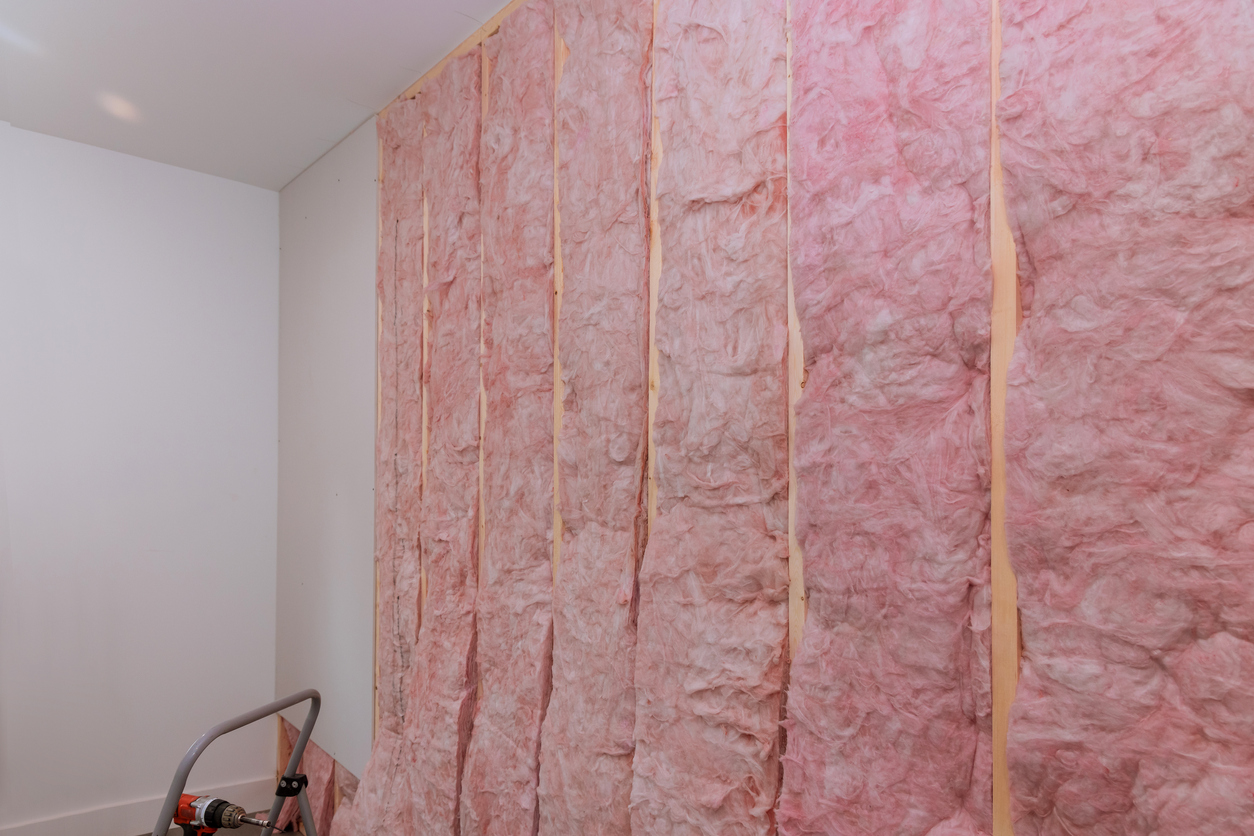
Pro: Cost is the lowest among insulation types.
Batts are pre-cut pieces of fiberglass, mineral wool, or cotton insulation fitted between studs, joists, or rafters. In old homes, they are often used in open attics. This type of insulation is relatively inexpensive. It’s easy to install and does not require a professional. Providing a moderate R-value, batts are useful in preventing fires, moisture, and mold. Their effectiveness increases when combined with other types of insulation, such as rigid foam.
“You generally can’t go wrong by sticking to the ordinance code for the city and using a basic paper-covered fiberglass if you have the room,” says Zazera. “In Pittsburgh, you have to be aware of the stud size. If you have 2x4s, use R21; if you have 2x6s, use R29. In attics, I use R39, which is 12 to 15 inches thick because you have the space and room.”
Con: Heat leakage can occur between batts.
While it can be cut to fit in odd spots, their rectangular-cut shape means that they do not provide uninterrupted coverage, allowing leakage in irregular areas. Over time, they can compress or sag, losing effectiveness. The fine fibers can also irritate the eyes, skin, and lungs, requiring protective equipment during installation.
Reflective or Radiant Barrier Systems
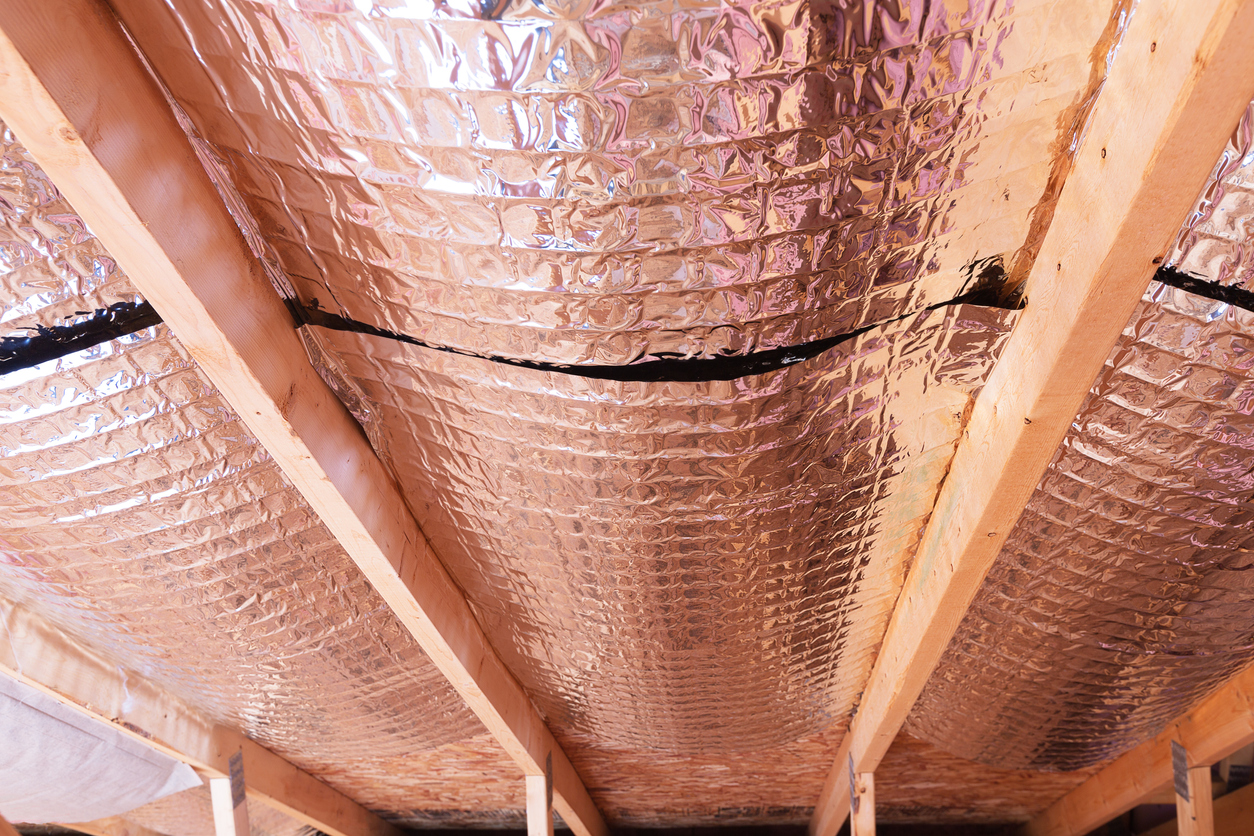
Pro: Radiant barrier enhances insulation’s effectiveness.
A lightweight, affordable insulation, reflective (radiant) barrier systems are easy to install. Depending on usage and product type, it is made with reflective foil-faced kraft paper, plastic film, polyethylene bubbles, or cardboard. Like batts, it is often used between wood studs, rafters, and beams or applied to ceilings and floors. The ease of use and reflective quality that keeps heat in are advantages.
Con: Not very effective on its own.
Radiant barrier systems don’t typically replace another type of insulation, and are usually used in conjunction with another kind of insulation. On its own, the R-rating is not as effective as other residential options.
Rigid Foam Board Insulation

Pro: Inexpensive and effective in open areas.
DIYers often use this inexpensive insulation type to replace existing insulation. Often made of polystyrene, rigid foam board insulation is easy to use and its high thermal resistance are particularly effective in reducing heat conduction in unfinished attics or insulating basements.
Con: Difficult to use in hard-to-reach spaces.
The stiff nature of rigid foam board insulation makes it impractical for smaller, irregular, or hard-to-get-to spaces. Also, with its typical full length of 8 feet, it is cumbersome to move around when a homeowner installs foam board insulation.
Recycled and Eco-Conscious Insulation
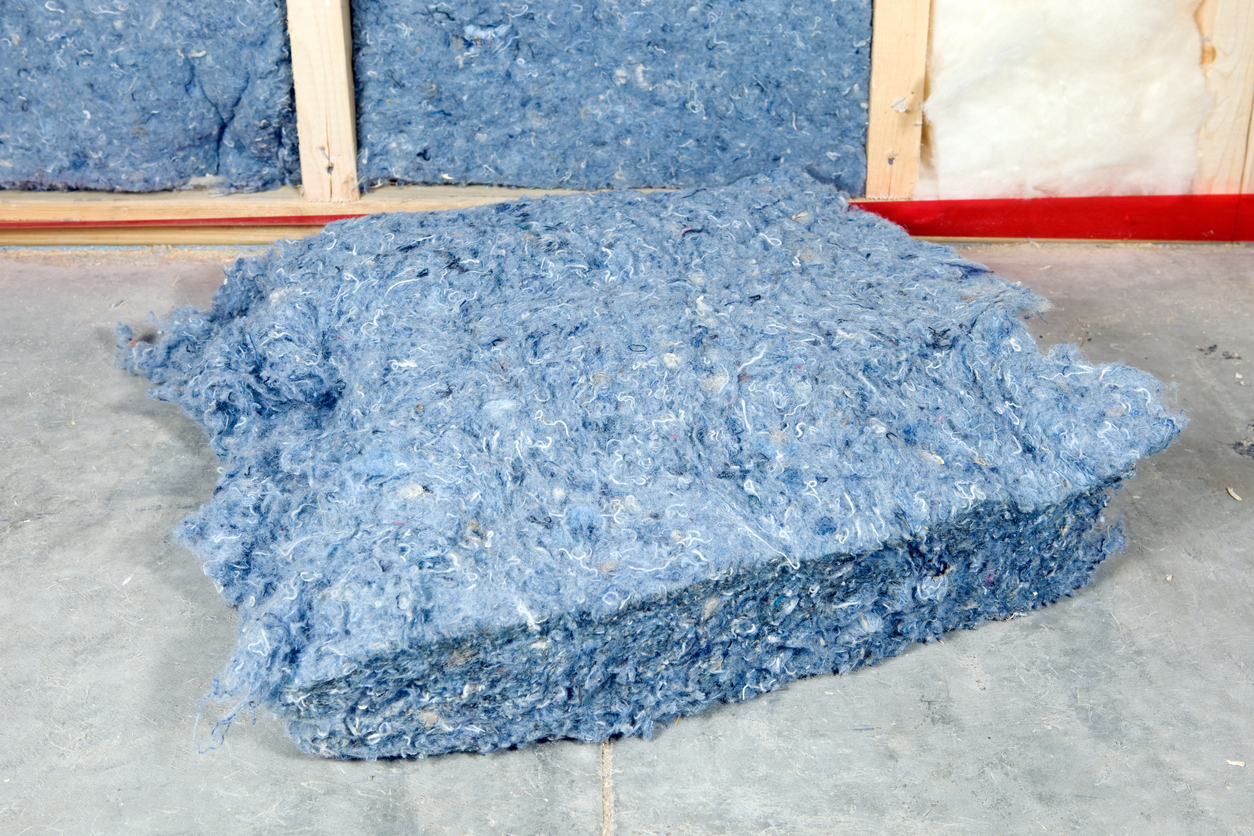
Pro: Ecologically sound option that reduces construction waste.
Recycled insulation often consists of denim that’s made of old jeans, denim cotton, or natural fibers like straw, hemp, and sheep’s wool. It is available in various forms, including batts, rolls, and loose-fill. The obvious pros are helping to reduce the ecological impact and waste created by the construction industry.
Con: Expensive insulation that may require more frequent replacement.
Generally more expensive than other types of insulation, there’s also a performance concern with some recycled insulation. Certain eco-friendly insulation types can lose their shape faster than regular fiberglass insulation, which decreases the product’s effectiveness and may require more regular updating, too.