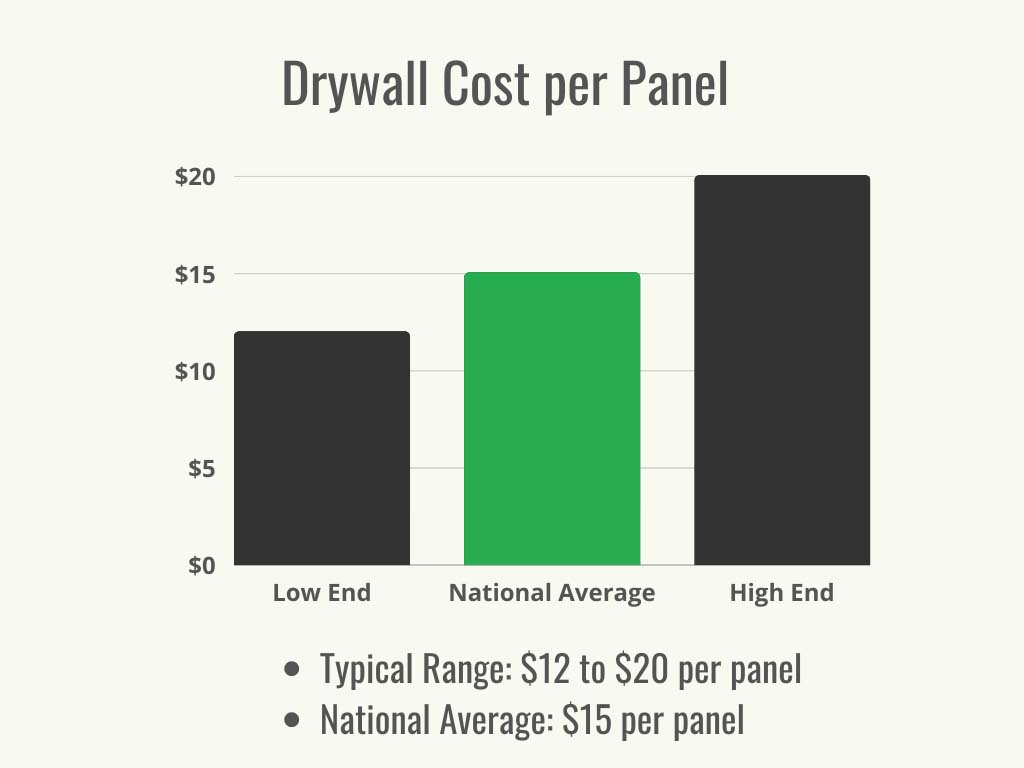
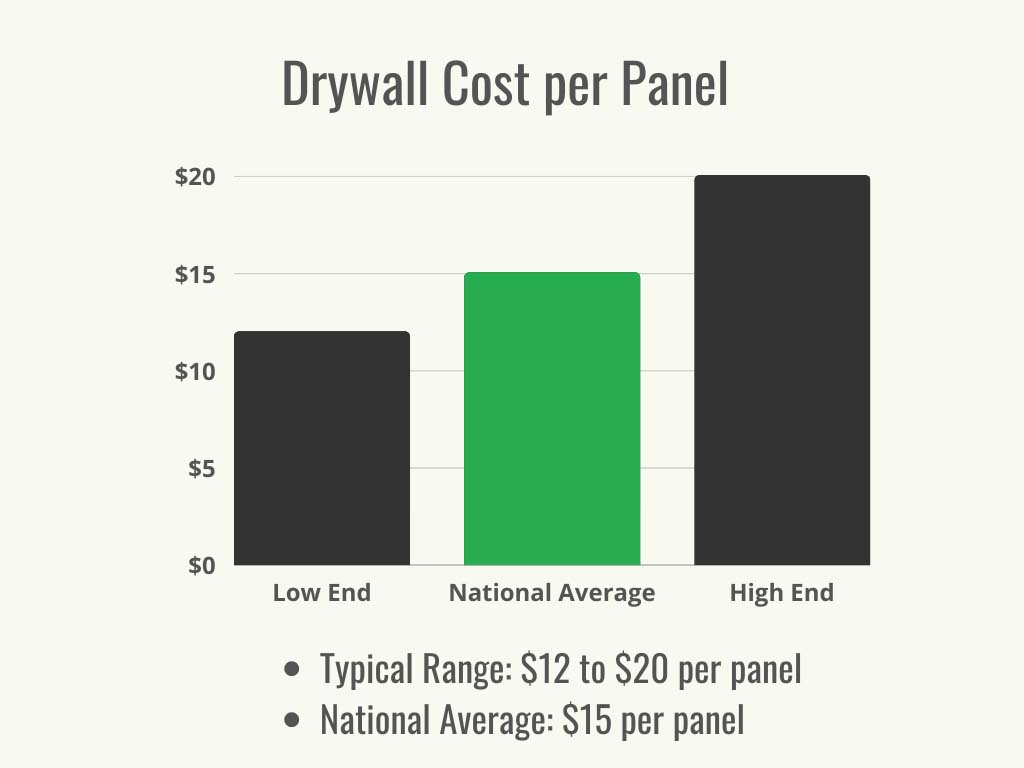
We may earn revenue from the products available on this page and participate in affiliate programs. Learn More ›
- Typical Range: $12 to $20 per panel
- National Average: $15 per panel
Glancing around a home, visitors take in the artwork, photographs, furniture, and even the paint color. The finish on the walls and ceilings underneath the paint doesn’t necessarily draw the eye—unless it’s cracked, slumped, or poorly patched. Drywall is the foundation of most modern walls and ceilings and the replacement product of choice for many older homes. A well-installed smooth or textured surface lets the furnishings and decor in any home shine.
Whether a homeowner is choosing a qualified contractor or learning how to hang drywall themselves, they’ll want to begin with an understanding of the different types of drywall available, the many factors that affect the overall cost of drywall, and the supplies needed to install it. How much does drywall cost? According to Angi and HomeAdvisor, the typical cost of drywall itself is between $12 and $20 per panel, with a national average of $15. Some additional costs are obvious, such as the ones for panels, screws, tape, mud, and joint compound, but other components, such as demolition, transportation, permits, and even the volume of sandpaper needed to get the job done well, might escape notice. In addition, there are several types of drywall available that can provide soundproofing, waterproofing, and fire resistance, along with more basic styles that support tile or shiplap walls. A variety of finishes can complement the style of the home and reduce the cost overall. To make these decisions easier, it’s a good idea for homeowners to calculate the cost of drywall panels and installation.
How to Calculate Drywall Cost
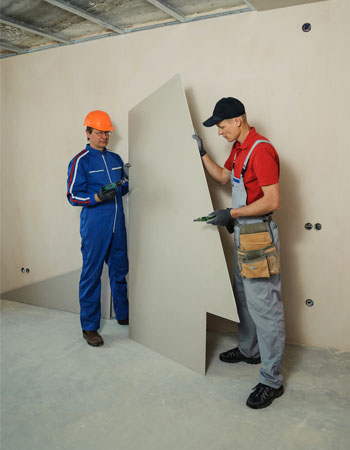
Calculating the overall cost of installing drywall in a home is a straightforward formula, but it does include a number of variables and decisions on the part of the homeowner. The following formula can help a homeowner calculate the amount of drywall needed for a project and the total cost.
- Measure the square footage (width times height) of the area that needs to be drywalled, then divide by 32 (if using 4-by-8-foot sheets) or by 48 (if using 4-by-12-foot sheets) to determine how many panels of drywall will be needed.
- Add the cost of a half-gallon of ready-mix compound per 100 square feet.
- Add the cost of 40 feet of drywall tape per 100 square feet.
- Add the cost of drywall screws: In general, 3 pounds of drywall screws will cover approximately 1,000 feet.
On average, it will cost between $200 and $300 to purchase enough drywall panels for a 12-foot-by-12-foot room. There are, of course, additional factors in calculating the overall material costs, including the number of odd cuts that create additional waste, corners, and the type and thickness of the panels themselves, but this formula should provide homeowners with a good estimate of how much material they’ll need to get started. It may also be useful for homeowners to plug these numbers into an online drywall calculator for a specific estimate.
Factors in Calculating Drywall Cost
While the math of calculating drywall cost is relatively easy to do, there are significant variables in the figured cost of hanging drywall in any given space. Because drywall is used in so many different areas of the home, there are varieties in the shape, thickness, and additional materials incorporated into the panels that create a wide cost range. In addition, regional considerations, including local construction booms, weather and transportation concerns, and even the season, can affect local pricing to make it vastly different from the national average drywall cost. There are some concrete factors, however, that are determined by the homeowner and provide an opportunity to save a little money.
Panel Size
Drywall panels come in standard sizes of 4 feet by 8 feet or 4 feet by 12 feet. Depending on the size and dimensions of the room, one panel size may be more efficient for the space and will create less waste than the other. While 4-by-12-foot sheets are a bit more expensive, the homeowner may need fewer sheets overall if their ceilings are high, which can save money along with time needed for cutting and taping.
Installation Location
The location where drywall is being installed will affect the overall cost. This is due to both the square footage of the room and the type of drywall that will be used. The cost to drywall smaller rooms, such as bathrooms, is lower overall—between $430 and $500—but the price per square foot may be higher. Often, green or purple boards are used instead of standard drywall for bathrooms because they are more moisture-resistant, and this can increase the cost. A room with larger square footage, such as a living room, will cost about $960 to $2,800 to drywall. The cost per square foot for basements and garages may be less because these areas are not typically finished with the same high-quality materials that are used for living spaces.
Drywall Thickness
Drywall is available in four thicknesses: ¼ inch, ⅜ inch, ½ inch, and ⅝ inch, with cost increasing with thickness. The cost for ¼-inch drywall is about $10 to $12 per sheet, and this type is mostly used for repairs to fortify existing walls. The cost of ⅜-inch drywall can run up to $15 per sheet; this type is mostly used when ½-inch drywall is too large for an existing space. Half-inch drywall is ideal for almost all spaces and can cost anywhere between $10 and $20 per sheet. The thickest drywall is ⅝ inch, and this type is almost exclusively used for soundproofing. It costs about $13 to $75 per sheet. Choosing the correct thickness for the project can help lower the overall cost.
Labor
Depending on the application of the drywall, hiring a qualified professional drywall hanger may be the best bet. Hanging and finishing drywall are two separate costs: The average cost to hang drywall is $0.15 to $0.65 per square foot. Taping and mudding drywall after it’s hung can range from $0.40 to $0.70 per square foot, while sanding and priming costs between $0.10 and $0.50 per square foot. The cost to finish the drywall ranges from $0.50 to $1.15 per square foot. Combining these costs gives a total drywall installation cost range of $1.15 to $3 per square foot.
Finishing
Drywall finishing is rated from level 0 to level 5. What follows are the finishing ratings and their typical costs.
- Level 0. A level 0 finish job means the drywall is screwed into the studs: No mudding or taping has been done. This service costs between $0.30 and $0.80 per square foot.
- Level 1. Level 1 includes mudding and taping the seams and costs between $0.70 and $1.50 per square foot for labor. Level 1 is not a complete finish and is common for attics and basements.
- Level 2. Level 2 adds a skim coat of joint compound. This finish is not usually suitable for a living space, but it’s more complete than a level 1 finish. Level 2 finishing costs $0.80 to $1.75 per square foot.
- Level 3. Level 3 adds a complete coat of joint compound and sanding. This finish costs $0.90 to $2.50 per square foot.
- Level 4. Level 4 results in drywall that is smoothed, sanded, and primed, but it may have surface imperfections. This finish is a good base for tiling or wallpaper, but is also suitable simply for painting. Level 4 finishing costs between $1 and $3 per square foot.
- Level 5. A level 5 drywall finish includes a full, smooth coat of joint compound over the entire wall along with primer that has been sanded. The drywall is ready for even glossy paint, as there are almost no imperfections. Level 5 finishing costs $1.15 to $3.50 per square foot.
Each degree of finish adds to the total cost of installation. If a homeowner prefers a hand- or spray-finished texture, such as rosebud, swirl, skip trowel, or orange peel, these can be added prior to a level 5 finish, which can reduce overall finish costs. These textures will add to the finishing cost, however, as they add to material and labor costs.
Geographic Location
Drywall prices can vary greatly depending on a homeowner’s region of the country. Prices tend to be lower in midwestern states. For example, prices in Ohio range from $7.85 to $12.10 per panel, whereas homeowners in California will pay between $11.85 and $19.80 per panel. On the East Coast, drywall costs average about $10.35 to $17.50 per panel.
Project Scope
Surprisingly, it can be more expensive per square foot to drywall a small room than a larger one. Covering a larger area provides more opportunities to use full sheets or scraps to fill interrupted walls, so the overall cost drops. It is least expensive when homeowners decide that hanging drywall in the entire house all at once is the best plan. But the cost isn’t only dependent on the total area mathematically: The number of cuts, fitting, and level of finish will also play into the total. Use (and therefore cost) of finishing materials will increase with a higher number of corners and specialized cuts, as corners require a special bead to be tidy. In addition, some drywall contractors may charge a minimum service fee, which could exceed the actual cost of installing drywall in a small space, so bundling several rooms into one project may help you save overall. This fee may also apply if only a small portion of existing drywall is being patched, which costs about $100 on average.
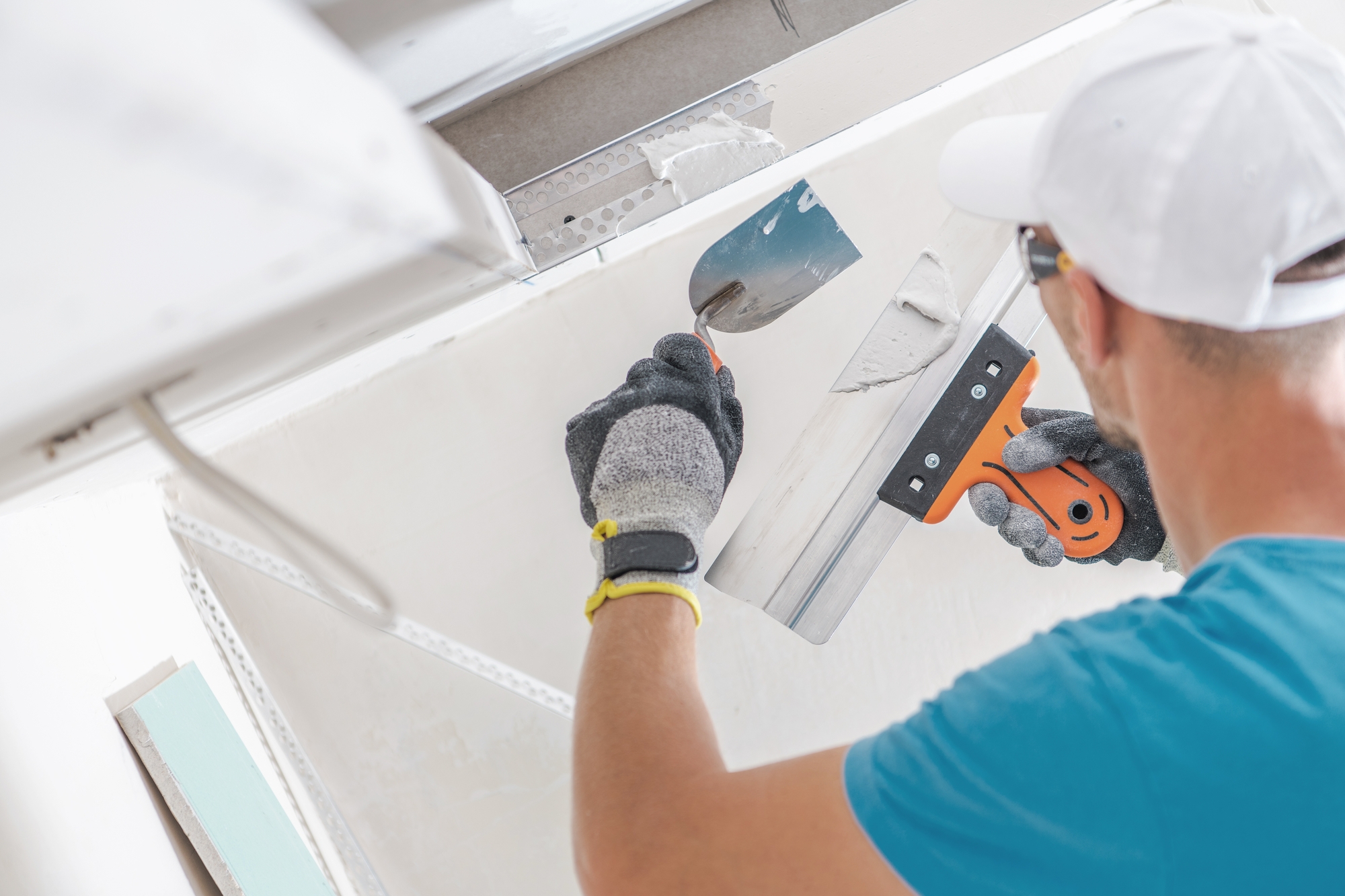
Additional Costs and Considerations
Having established the cost of the drywall materials needed for a project, homeowners may think they know how much they’re budgeting and are ready to head to the home improvement store to get started—but there are other cost considerations to factor in first.
Old Drywall Removal
A cost that many homeowners forget to include is the demolition cost of walls that are being removed and replaced. While some popular home shows make this part of the job seem like a fun, stress-reducing exercise that employs the strength of a hammer, in real renovation scenarios, it’s critical to be careful: Repairing damage to electrical outlets, wiring, plumbing, and other home system components in the wall will add significantly to the overall cost. For a non-load- bearing wall, demolition can cost as little as $1,200, but for load-bearing walls that require the rerouting of systems, it can cost as much as $5,000.
Insulation
For new walls, or walls on the exterior of the home that have been fully removed prior to the new drywall being added, homeowners will need to include the cost of materials and installation of insulation to maintain the energy efficiency of the building. Depending on the type of insulation the homeowner chooses, costs can range from $0.65 to $6.50 per square foot with professional installation.
Texture Application
Applying texture to drywall is a simple way to add visual interest to a room. Texture can be applied to both walls and ceilings in a wide variety of styles depending on the homeowner’s preference. Some textures like Santa Fe and skip trowel have a rustic appearance that is similar to stucco and can be applied by hand. The cost for hand-applied textures is between $1.50 and $2 per square foot. Knockdown and orange peel textures are more subtle and can be applied with a spray. Spray textures are more affordable since they are quicker and easier to apply, and these cost between $0.50 and $1 per square foot.
Customization
Drywall panels are available with water resistance, waterproofing, soundproofing, and with and without paper—there is a type of drywall for almost every application, and the costs vary significantly based on which additional features are required.
Permits
Do homeowners need a permit to add or replace drywall? In the case of a simple replacement to clean up a damaged wall, probably not. If the drywall project involves plumbing, electrical work, or a load-bearing wall, or if the location of a wall will change, it’s important for homeowners to check with their local municipality to see if a permit and inspection are required.
Asbestos Removal
Any homeowner living in an older house has likely learned to ask the asbestos question before disturbing existing materials. Asbestos can be present in older plaster walls, tile, and tile adhesive, especially in homes built before 1980, and it can cause serious illness and lung damage if it’s released into the air and inhaled. For homes built before 1980, it’s important to assess the likelihood that asbestos is present, test for it, and have it removed (at a cost of $1,200 to $3,000) before proceeding.
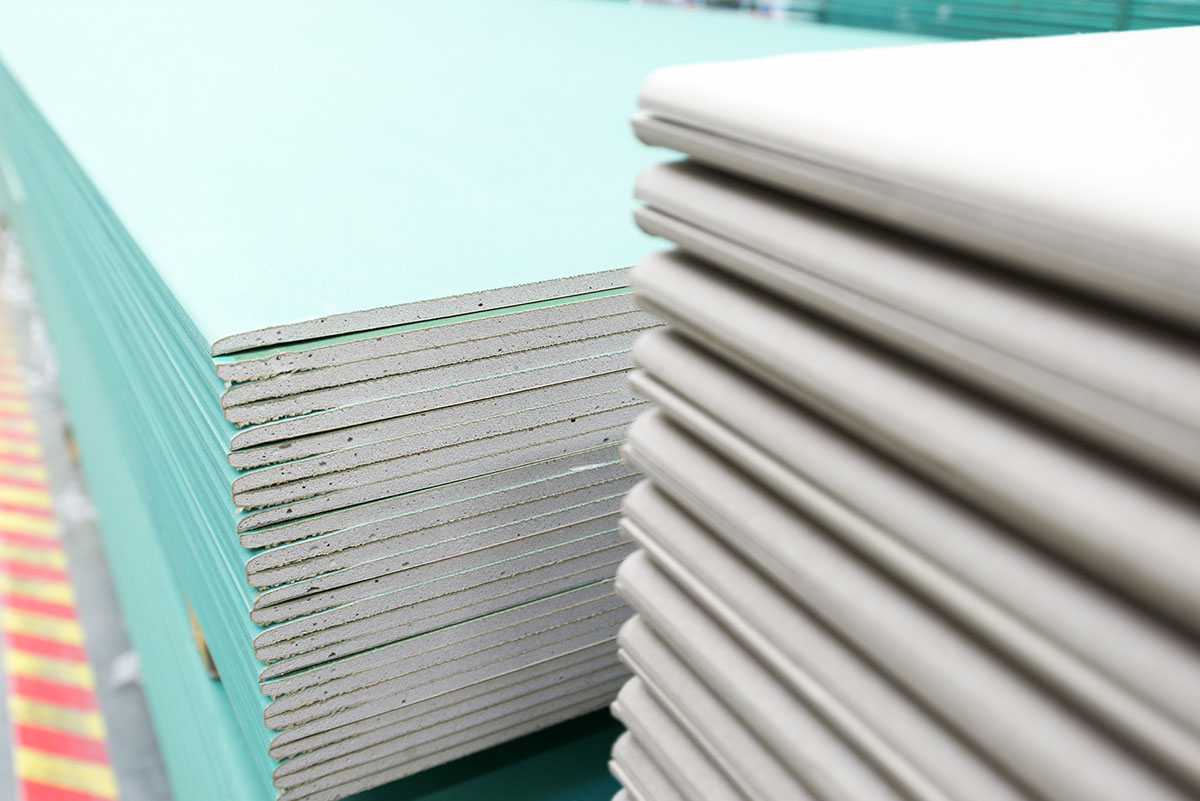
Types of Drywall
Drywall is a catchall term that many people use to describe any wallboard product. However, as drywall has become the standard product for wall and ceiling installations, additional styles and formulations have been developed to meet the needs of different purposes and spaces. Each additional component adds to the cost per panel, but it’s important to choose the best panel for the space in which it will be installed.

Regular
Regular drywall, which is gypsum board sandwiched between two paper layers for stability, is the least expensive option. It’s fine for most bedroom, living room, and dining room walls where moisture resistance is not a key concern. The price per panel will vary based on the panel size and thickness, but it ranges from $15 to $20.
Green Board
Green board drywall adds an extra layer of green material on the outside surfaces of the board, making it water-resistant. Ideal for areas in the home where moisture may be a concern, but not for walls that need to be completely waterproof, green board is often used in kitchens or where it will be covered with tiles and grout. Green board comes in a standard 4-by-8-foot size, and costs range from $14 to $18 per panel.
Blue Board
Blue board drywall uses a different kind of paper to sandwich the gypsum. The blue paper has a smoother finish that holds finish plaster on top, allowing the installer to build a perfectly smooth, seam-free finish. It should not be used with mud, tape, and joint compound. Prices range from $12 to $15 per panel.
Purple
While green board drywall has some moisture resistance, purple drywall offers superior moisture and mold resistance, making it even more effective in situations where dampness, moisture, and water contact may be factors. It can be used in all wall and ceiling applications, but it’s especially effective in moist conditions. Some purple board includes soundproofing and additional fire resistance, so it’s important that homeowners know exactly what they or their contractors are purchasing. Cost ranges from $15 to $60 per panel.
Paperless
Paperless drywall is a newer addition to the drywall range. Covered with fiberglass instead of paper, this option protects the gypsum core from rot, moisture, and mildew and makes the board less likely to break and dent. It retains the texture of the fiberglass on the outside, so it may require additional joint compound to achieve a smooth finish. There are paperless versions of the different variations of drywall, so costs will likely be at the higher end of each range. On average, paperless drywall costs $25 to $35 per panel.
Type X
Type X is fire-resistant drywall. All gypsum board is by nature somewhat resistant to fire, but Type X features a denser pack of gypsum and noncombustible fibers. It is heavier and harder to cut. It comes in ⅝-, ½-, and ¾-inch thicknesses, but the ¾-inch size can be difficult to find. To achieve Type X certification, a ⅝-inch board has to meet a 1-hour fire-resistance rating, and a ½-inch board must meet a ¾-hour rating. Type X can be layered for additional resistance, which also adds soundproofing. Ideal for garages and basements, along with applications in buildings that must meet certain building codes, Type X drywall ranges from $20 to $30 per panel.
Soundproof
While the density of all drywall panels offers some soundproofing, choosing a board designed to be soundproof adds an extra layer of defense against noisy neighbors, televisions, construction work-related sounds, and more. Soundproof drywall, which is often used in music rooms, between apartments, and in other places where noise is a problem or silence is required, is a laminated drywall that includes wood fibers, gypsum, and other polymers to reduce sound transfer. It is a dense product that can be difficult to work with, but it achieves a quieter atmosphere. The cost per panel ranges from $40 to $55.
Eco-Friendly
Eco-friendly drywall is characterized by its recyclability and high content of post-consumer materials. Usually made from gypsum, eco-friendly drywall is lightweight and durable. The cost of eco-friendly drywall is around $19 to $27 per panel.
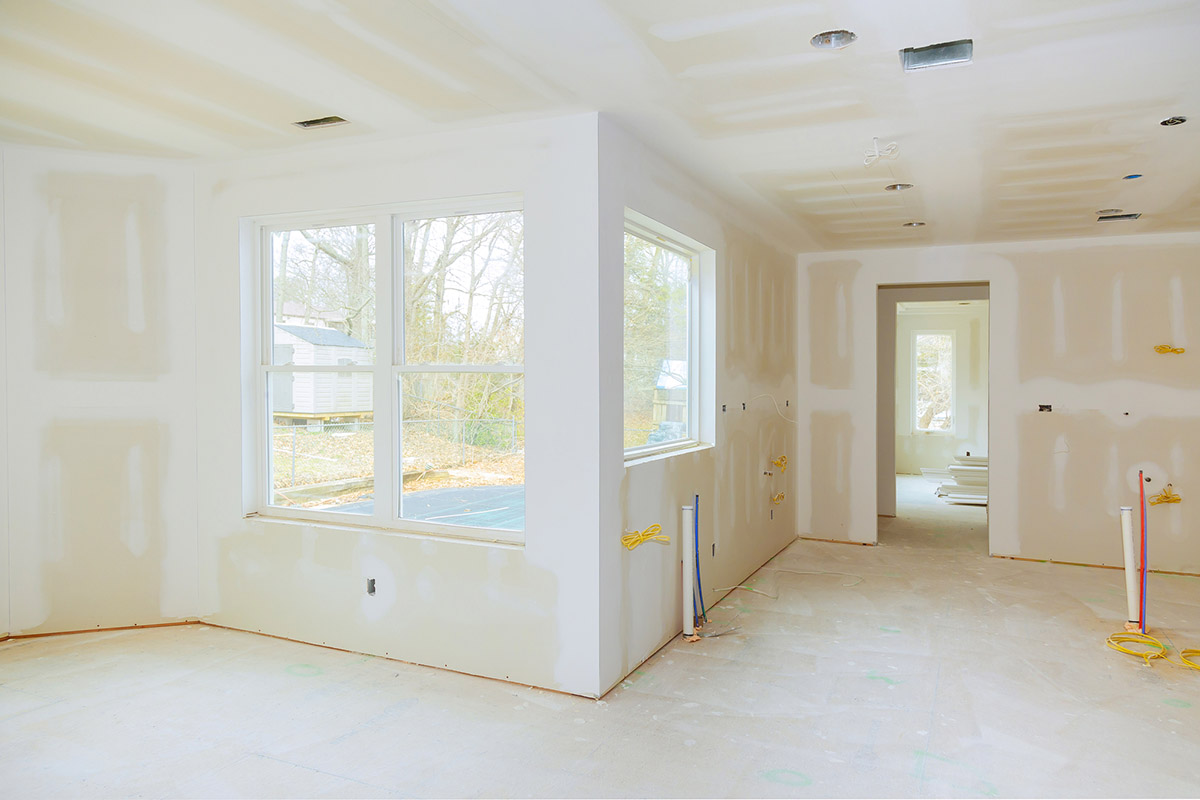
Benefits of Choosing Drywall
For homeowners who are considering a remodel or removing or adding walls to their home, the options can seem overwhelming. For those living in older homes, the first instinct may be toward plaster, as it is a traditional and attractive finish. Modern drywall, however, is significantly less labor-intensive to install and is generally easier to maintain. It can even add energy efficiency to the home.
Easy Installation and Building
Drywall is relatively easy to install. The boards are cut, then screwed into wall studs. Tape and joint compound are applied over seams and screws, then sanded. While it takes practice and skill to get the taping just right, it can potentially be a DIY project for experienced homeowners. Plaster, on the other hand, requires specialized building experience to attach the wood laths to the studs. Then layer after layer of plaster must be applied to the lath and finished. When comparing drywall vs. plaster, labor costs alone can be more than three times than those to install drywall. While plaster can be a great option for a single wall repair if the other walls remain intact, drywall is the easier path to take for larger or whole-room projects, and once painted, most people won’t know the difference.
Ease of Repair
Whether they are dented and scratched during a move, discolored by water exposure, or dotted with holes from nails, walls are bound to undergo damage during their lifetime. Drywall repair is generally affordable, which is a significant advantage. Small dents or holes can be filled with spackle and repainted. Even major damage is easy to repair by simply replacing the affected panels. Drywall repair costs by a professional are relatively affordable, and some homeowners may even be able to do the repairs themselves.
Energy Efficiency
Layers of paper, gypsum, and other fibers give drywall outstanding energy efficiency. When used in the walls of homes and apartments, it can keep interiors cooler in the summer and warmer in the winter, and thus help keep energy bills down.
Fire Resistance
Gypsum is naturally fire-resistant, which can help prevent fire from spreading from room to room. In addition, the insulation properties of drywall can keep the heat from spreading through the walls. Drywall can keep fires from spreading and buy occupants valuable time to get out, get help, and extinguish the fire before it damages more of the home’s structure.
Customization Options
The many varieties of drywall offer benefits for different applications. Whether the homeowner is looking for waterproofing, soundproofing, fireproofing, or dent resistance, there are choices that make it easy to pick the right drywall for each installation. In addition, a skilled contractor can add hand finishes or spray finishes to the drywall, allowing homeowners to choose distinctive textures and finishes for a truly custom product.
Cost-Efficiency
Jobs such as installing, maintaining, and repairing drywall are some of the most affordable that can be done on the home. The ability to replace or repair small sections without extensive finish work keeps the maintenance costs down, and the costs of drywall materials themselves are on par with, or less than, the costs of plaster and other options. The installation costs can be minimal for a DIYer, and even hiring a professional to do the job is generally more affordable than the cost of the more labor-intensive plaster workers.

Drywall Installation: DIY vs. Hiring a Professional
For some handy homeowners, figuring out how to hang drywall is a task that can be done to completion: Measuring, cutting, and screwing the boards into the wall isn’t intrinsically difficult. However, figuring out how to install drywall effectively is a different challenge. Taping looks simple on television, but determining how much mud to scoop onto a trowel and achieving the exact correct wrist angle to smooth it down, leaving just enough on the wall to seal the tape but not so much that it never dries, is a skill developed through years of experience. This is also true for smoothing a coat of joint compound across a wall without leaving seams and ridges. A professional will help make the process more efficient, which will result in a more polished product.
While a homeowner may know a few basics of how to fix drywall, larger-scale work is often better left to a professional. Large holes or water damage require heavy-duty repairs beyond patching and spackling. Drywall cracks and large gaps should not be ignored, as they can be indicative of a shifting foundation. A professional understands these warning signs and will have advice on how to proceed. Homeowners will also want to consider that drywall panels are heavy; this is especially true for ceiling installations, and special equipment may be necessary to support the materials. With the money saved by avoiding repeated trips to the home improvement store for more drywall tools, homeowners may find that hiring a professional to complete the installation is less expensive than a DIY approach.
How to Save Money on Drywall Cost
While drywall is one of the most affordable options to finish walls and ceilings, the cost is not insignificant. Because there are so many choices in terms of type of board, installation options, and finishes, there are some ways the savvy homeowner can bring the overall cost down.
- Budget and estimate carefully from the beginning. Buying all the supplies at once may earn you a discount, and hiring electricians or plumbers ahead of time can be less expensive than an emergency call.
- Purchase supplies from a drywall supplier instead of a big-box store. Drywall suppliers know their products, can help you estimate better, and will often reduce the price for a bulk order. In addition, this approach means you’ll likely spend less on impulse purchases at a home improvement store.
- Don’t opt for the cheapest material. Even though it will save money up front, low-quality drywall will need to be repaired or replaced much more frequently. The cost will catch up with you eventually.
- Remove the existing wall surface yourself. This can save money on demolition if you are confident that your walls do not involve asbestos or lead paint. Do this carefully and slowly, with awareness of electrical and plumbing components that may be behind the walls. If you know how to cut drywall and have the best tools to cut drywall, consider doing the hanging yourself and hiring a pro to handle the rest.
- Choose a textured finish over a smooth one. There are several levels of finish, and a perfectly smooth finish is more expensive than a mildly textured one.
Ask the contractor about taping options. Standard seaming tape is less expensive than self-adhesive tape, but the seaming tape can require more layers of compound, which can ramp up the cost.
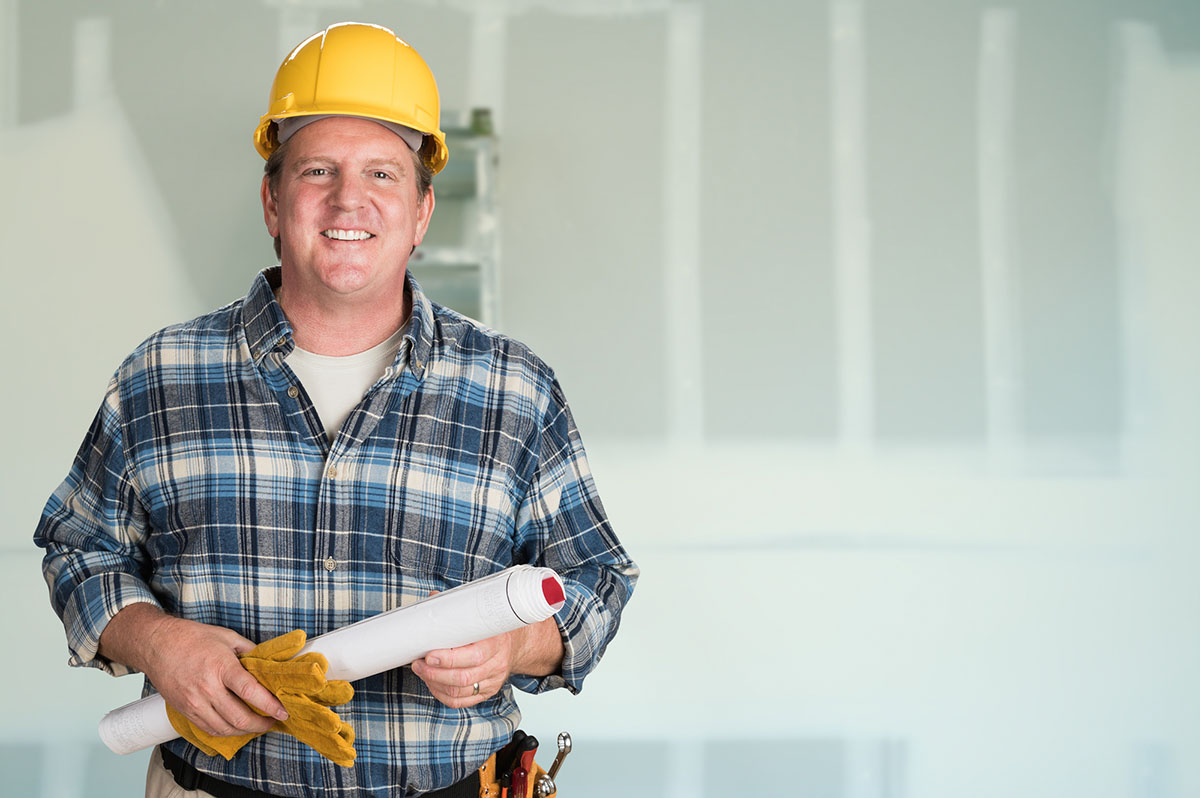
Questions to Ask About Drywall Installation
As homeowners are researching “drywall contractors near me,” they’ll want to look for someone who has specialized in drywall for a long time. An experienced drywall company will be able to provide more accurate estimates and will help the homeowner avoid the markup a general contractor can add to a smaller project. It’s important for homeowners to request a written contract and ask some questions to help keep the cost as close to their budget as possible.
- Does your estimate include the costs of transportation, demolition and preparation, materials, cleanup, and removal of dust and debris?
- What are my options for the type of drywall, and how do they affect the cost?
- What is your timeline for the process? Can I get that in writing?
- How long have you been in business?
- Do you have any references?
- Who will be my point of contact during the project?
- Will you need any permits? Who is responsible for acquiring them?
- Can I see samples of the options for finish texture?
- What deposit do you require?
- Are you licensed and insured?
- Who will be working with you, and are they also licensed and insured?
- What warranty do you provide against seam cracks and slumps?
- What payment methods do you accept, and what is the payment schedule?
- Do I need to make any preparations prior to your arrival?
FAQs
There are so many components to the cost of drywall that it can become overwhelming. The answers to these frequently asked questions can help homeowners zero in on how to best plan their drywall installation project.
Q. Why is drywall good for your house?
Drywall is an affordable, energy-efficient option for walls and ceilings that provides natural fire resistance and soundproofing. It’s easy to customize for the location in the home and to have the style and texture the homeowner wants. Drywall is easily painted and repainted without a lot of prep work, or it can be used as a strong foundation for tile or shiplap walls.
Q. How large a gap should be between sheets of drywall?
Drywall panels should never be snugged up against each other. Like all other porous building materials, they need space to expand and contract with heat and cold and to accommodate shifts and settling of the structure. A standard ⅛-inch gap between panels will be hidden from view by tape and mud but will reduce buckling and cracking after the job is done.
Q. How long does drywall last?
Drywall walls and ceilings last between 30 and 70 years. A quality installation with offset seams and good taping sets up a long-lasting job. House settling can occasionally cause cracking. Water leaks, damage, or excessive holes from wall hangings can weaken the structure of the board itself and of taped and mudded joints. Prompt repair of this kind of damage along with any cracks will extend the life of the wall.
Q. What’s the difference between sheetrock and drywall?
Sheetrock is a brand of drywall produced by United States Gypsum Corporation. In other words, all Sheetrock is drywall, but not all drywall is Sheetrock.
Q. What’s the difference between drywall and plaster?
Plaster was commonly used in homes until around the 1940s, and it’s made up of wooden slats that are coated with plaster. Plaster is generally considered to have a more polished look, but it is pricier and more difficult to install than drywall.